What is the Difference Between AC and DC Servo Motors?
Servo Motor
Servo motor also called control motors, are used in feedback control systems as output actuators and does not use for continuous energy conversion. The principle of the servomotor is similar to that of the other electromagnetic motor, but the construction and the operation are different. Their power rating varies from a fraction of a watt to a few hundred watts. Rotor inertia of the motors is low and have a high speed of response. The rotor of the Motor has the long length and smaller diameter. They operate at very low speed and sometimes even at the zero speed. Servo motor is widely used in radar and computers, robot, machine tool, tracking and guidance systems, processing controlling.
AC Servo Motor
Servo motors are generally an assembly of four things: a DC motor, a gearing set, a control circuit and a position-sensor (usually a potentiometer). The position of servo motors can be controlled more precisely than those of standard DC motors, and they usually have three wires (power, ground & control). AC Servo Motors are divided into two types 2 and 3 Phase AC servomotor. Most of the AC servomotor are of the two-phase squirrel cage induction motor type. They are used for low power applications. The three phase squirrel cage induction motor is now utilized for the applications where high-power system is required. An AC servo motor is essentially a two-phase induction motor with modified constructional features to suit servo applications as shown in figure 1.
It has two windings displaced by 90° on the stator. One winding, called as reference winding, is supplied with a constant sinusoidal voltage. The second winding, called control winding, is supplied with a variable control voltage which is displaced by--90°out of phase from the reference voltage.
The major differences between the normal induction motor and an AC servo motor are
1. The rotor winding of an ac servo motor has high resistance (R) compared to its inductive reactance (X) so that its X / R ratio is very low.
2. For a normal induction motor, X / R ratio is high so that the maximum torque is obtained in normal operating region which is around 5% of slip.
The torque speed characteristics of a normal induction motor and an ac servo motor are shown in figures 2.

The torque-speed characteristic of a normal induction motor is highly nonlinear and has a positive slope for some portion of the curve. This is not desirable for control applications. as the positive slope makes the systems unstable. The torque speed characteristic of an ac servo motor is fairly linear and has negative slope throughout. The rotor construction is usually squirrel cage or drag cup type for an ac servo motor. The diameter is small compared to the length of the rotor which reduces inertia of the moving parts. Thus, it has good accelerating characteristic and good dynamic response. The supplies to the two windings of ac servo motor are not balanced as in the case of a normal induction motor. The control voltage varies both in magnitude and phase with respect to the constant reference vulture applied to the reference winding. The direction of rotation of the motor depends on the phase (± 90°) of the control voltage with respect to the reference voltage. For different rms values of control voltage the torque speed characteristics are shown in Figure. The torque varies approximately linearly with respect to speed and also controls voltage. The torque speed characteristics can be linearized at the operating point and the transfer function of the motor can be obtained.
DC Servomotor
A DC servo motor is used as an actuator to drive a load. It is usually a DC motor of low power rating. DC servo motors have a high ratio of starting torque to inertia and therefore they have a faster dynamic response. DC motors are constructed using rare earth permanent magnets which have high residual flux density and high coercively. As no field winding is used, the field copper losses am zero and hence, the overall efficiency of the motor is high. The speed torque characteristic of this motor is flat over a wide range, as the armature reaction is negligible. Moreover, speed in directly proportional to the armature voltage for a given torque. Armature of a DC servo motor is specially designed to have low inertia. DC Servo Motors are separately excited DC motor or permanent magnet DC motors. The figure (a) shows the connection of Separately Excited DC Servo motor and the figure (b) shows the armature MMF and the excitation field MMF in quadrature in a DC machine. This provides a fast torque response because torque and flux are decoupled. Therefore, a small change in the armature voltage or current brings a significant shift in the position or speed of the rotor. Most of the high-power servo motors are mainly DC.
(a)Armature controlled DC servo motor
The physical model of an armature controlled DC servo motor is given in.
The armature winding has a resistance Ra and inductance La.
The field is produced either by a permanent magnet or the field winding is separately excited and supplied with constant voltage so that the field current, if is a constant. When the armature is supplied with a DC voltage of ea volts, the armature rotates and produces a back emf, eb. The armature current ia depends on the difference of eb and en. The armature has a permanent of inertia J, frictional coefficient B0. The angular displacement of the motor is θ.
(b)Field controlled DC servo motor
The schematic diagram of a field controlled DC servo motor is shown in figure 4.

Servo motor also called control motors, are used in feedback control systems as output actuators and does not use for continuous energy conversion. The principle of the servomotor is similar to that of the other electromagnetic motor, but the construction and the operation are different. Their power rating varies from a fraction of a watt to a few hundred watts. Rotor inertia of the motors is low and have a high speed of response. The rotor of the Motor has the long length and smaller diameter. They operate at very low speed and sometimes even at the zero speed. Servo motor is widely used in radar and computers, robot, machine tool, tracking and guidance systems, processing controlling.
AC Servo Motor
Servo motors are generally an assembly of four things: a DC motor, a gearing set, a control circuit and a position-sensor (usually a potentiometer). The position of servo motors can be controlled more precisely than those of standard DC motors, and they usually have three wires (power, ground & control). AC Servo Motors are divided into two types 2 and 3 Phase AC servomotor. Most of the AC servomotor are of the two-phase squirrel cage induction motor type. They are used for low power applications. The three phase squirrel cage induction motor is now utilized for the applications where high-power system is required. An AC servo motor is essentially a two-phase induction motor with modified constructional features to suit servo applications as shown in figure 1.

Figure 1 Symbolic representation of AC Servomotor
It has two windings displaced by 90° on the stator. One winding, called as reference winding, is supplied with a constant sinusoidal voltage. The second winding, called control winding, is supplied with a variable control voltage which is displaced by--90°out of phase from the reference voltage.
The major differences between the normal induction motor and an AC servo motor are
1. The rotor winding of an ac servo motor has high resistance (R) compared to its inductive reactance (X) so that its X / R ratio is very low.
2. For a normal induction motor, X / R ratio is high so that the maximum torque is obtained in normal operating region which is around 5% of slip.
The torque speed characteristics of a normal induction motor and an ac servo motor are shown in figures 2.

Figure 2 Torque speed characteristics of AC motors
The torque-speed characteristic of a normal induction motor is highly nonlinear and has a positive slope for some portion of the curve. This is not desirable for control applications. as the positive slope makes the systems unstable. The torque speed characteristic of an ac servo motor is fairly linear and has negative slope throughout. The rotor construction is usually squirrel cage or drag cup type for an ac servo motor. The diameter is small compared to the length of the rotor which reduces inertia of the moving parts. Thus, it has good accelerating characteristic and good dynamic response. The supplies to the two windings of ac servo motor are not balanced as in the case of a normal induction motor. The control voltage varies both in magnitude and phase with respect to the constant reference vulture applied to the reference winding. The direction of rotation of the motor depends on the phase (± 90°) of the control voltage with respect to the reference voltage. For different rms values of control voltage the torque speed characteristics are shown in Figure. The torque varies approximately linearly with respect to speed and also controls voltage. The torque speed characteristics can be linearized at the operating point and the transfer function of the motor can be obtained.
DC Servomotor
A DC servo motor is used as an actuator to drive a load. It is usually a DC motor of low power rating. DC servo motors have a high ratio of starting torque to inertia and therefore they have a faster dynamic response. DC motors are constructed using rare earth permanent magnets which have high residual flux density and high coercively. As no field winding is used, the field copper losses am zero and hence, the overall efficiency of the motor is high. The speed torque characteristic of this motor is flat over a wide range, as the armature reaction is negligible. Moreover, speed in directly proportional to the armature voltage for a given torque. Armature of a DC servo motor is specially designed to have low inertia. DC Servo Motors are separately excited DC motor or permanent magnet DC motors. The figure (a) shows the connection of Separately Excited DC Servo motor and the figure (b) shows the armature MMF and the excitation field MMF in quadrature in a DC machine. This provides a fast torque response because torque and flux are decoupled. Therefore, a small change in the armature voltage or current brings a significant shift in the position or speed of the rotor. Most of the high-power servo motors are mainly DC.
(a)Armature controlled DC servo motor
The physical model of an armature controlled DC servo motor is given in.
The armature winding has a resistance Ra and inductance La.

Figure 3 Armature controlled DC motor with load
The field is produced either by a permanent magnet or the field winding is separately excited and supplied with constant voltage so that the field current, if is a constant. When the armature is supplied with a DC voltage of ea volts, the armature rotates and produces a back emf, eb. The armature current ia depends on the difference of eb and en. The armature has a permanent of inertia J, frictional coefficient B0. The angular displacement of the motor is θ.
(b)Field controlled DC servo motor
The schematic diagram of a field controlled DC servo motor is shown in figure 4.

Figure 4 Field controlled DC servomotor
Post a Comment:
You may also like:
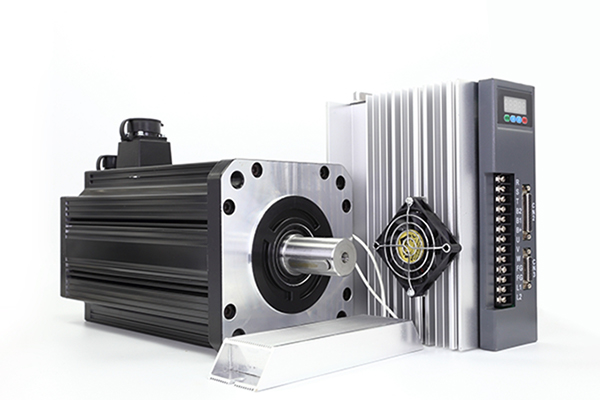
Category
Featured Articles
How to Test Servo Motor?
Servo motors are devices that convert electrical signals into mechanical motion and are widely used in industrial automation, ...

What is a Servo Motor?
There are some special types of application of electrical motor where rotation of the motor is required for just a certain angle ...
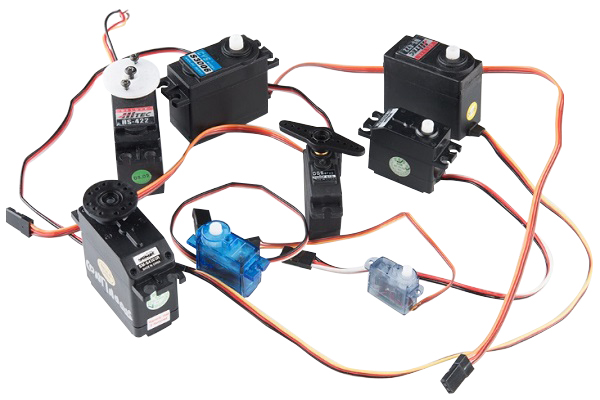
How to Maintain Servo Motor?
Servo motors play a crucial role in various industries, serving as precision control devices in applications ranging from ...

What are the Types of Servo Motor?
There are some special types of application of electrical motor where rotation of the motor is required for just a certain angle ...

How to Select the Suitable Power ...
It's important to consider the unique demands of a motion control application when selecting a power supply. During ...
