Home » FAQ
Servo Motor also called control motors, are used in feedback control systems as output actuators and does not use for continuous energy conversion. The principle of the Servomotor is similar to that of the other electromagnetic motor, but the construction and the operation are different. Their power rating varies from a fraction of a watt to a few hundred watts. Rotor inertia of the motors is low and have a high speed of response. The rotor of the Motor has the long length and smaller diameter. They operate at very low speed and sometimes even at the zero speed. Servo motor is widely used in radar and computers, robot, machine tool, tracking and guidance systems, processing controlling.

There are some special types of application of electrical motor where rotation of the motor is required for just a certain angle not continuously for long period of time. For these applications, some special types of motor are required with some special arrangement, which makes the motor to rotate a certain angle for a given electrical input (signal). This is normally a simple motor, which is controlled for specific angular rotation with the help of additional servomechanism (a typical closed loop feedback control system). Servo motor is a special type of motor which is automatically operated up to certain limit for a given command with help of error-sensing feedback to correct the performance.
Each technology has its niche, and since the selection of either of these technologies for a given application affects its chance of success, it is important for the machine designer to select the best motor-drive system for the application, while considering the technical advantages and disadvantages of both. It is all about utilizing these technologies with balance to achieve the desired process performance for a given machine design while balancing cost versus the capability of the required mechanism.
This article presents an overview of different baseline capabilities for selection criteria between stepper and servo technology. A thorough understanding of these technologies will help generate the best and most efficient mechatronic designs to bring forth the full capability of a machine.
Today’s digital stepper motor drives provide enhanced drive features, option flexibility, and communication protocols using advanced integrated circuits and simplified programming techniques. The same is true of servo motor systems, while higher torque density, improved electronics, algorithms, and higher feedback resolution have resulted in higher system Bandwidth (BW) capabilities, and lower initial and overall operating costs for many applications.

This article presents an overview of different baseline capabilities for selection criteria between stepper and servo technology. A thorough understanding of these technologies will help generate the best and most efficient mechatronic designs to bring forth the full capability of a machine.
Today’s digital stepper motor drives provide enhanced drive features, option flexibility, and communication protocols using advanced integrated circuits and simplified programming techniques. The same is true of servo motor systems, while higher torque density, improved electronics, algorithms, and higher feedback resolution have resulted in higher system Bandwidth (BW) capabilities, and lower initial and overall operating costs for many applications.
A servo is a mechanical motorized device that can be instructed to move the output shaft attached to a servo wheel or arm to a specified position. Inside the servo box is a DC motor mechanically linked to a position feedback potentiometer, gearbox, electronic feedback control loop circuitry and motor drive electronic circuit. A typical RC servo looks like a plastic rectangular box with a rotary shaft coming up and out the top of the box and three electrical wires out of the servo side to a plastic 3 pin connector. Attached to the output shaft out the top of the box is a servo wheel or Arm. These wheels or arms are usually a plastic part with holes in it for attaching push / pull rods, ball joints or other mechanical linkage devices to the servo. The three electrical connection wires out of the side are V- (Ground), V+ (Plus voltage) and S Control (Signal). The control S (Signal) wire receives Pulse Width Modulation (PWM) signals sent from an external controller and is converted by the servo on board circuitry to operate the servo.
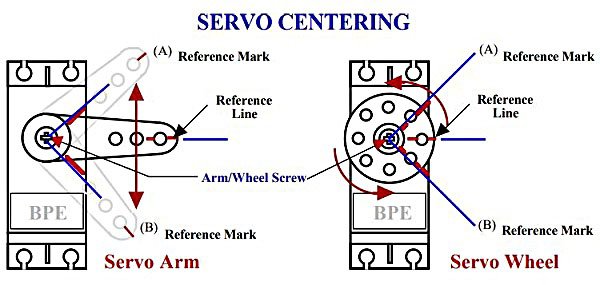
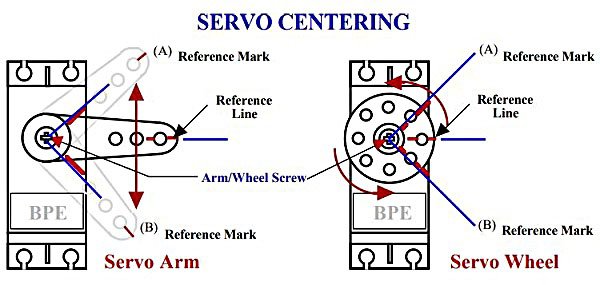
The importance of servo motor sizing should not be underestimated. Proper motor sizing will
not only result in significant cost savings by saving energy, reducing purchasing and operating costs, reducing downtime, etc.; it also helps the engineer to design better motion control systems. The servo motor represents the most influential cost factor in the motion control system design, not only during the purchasing process, but especially during servo operation. A high-torque motor will require a stronger and thus more expensive amplifier than smaller motors. The combination of higher torque motor plus amplifier results not only in higher initial expenses, but will also lead to higher operational costs, in particular increased energy consumption. It is estimated, that the purchase price represents only about 2% of the total life cycle costs; about 96% is electricity.
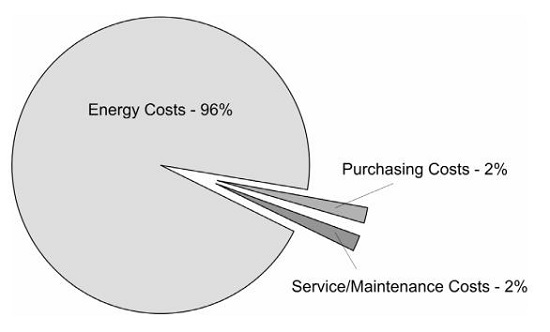
To verify the servo position, a marker is attached to the servo, and its orientation is measured by computer vision. A rough calibration target is used, explicitly avoiding any reliance on precise construction. Here, a simple piece of cardboard with a thin stripe is used.
The accuracy of the camera's measurements is verified by a series of physically measured positions. The deviation of these values from the camera measurement was less than the resolution of the physical measurements (1°) indicating that the visual measurement is consistent with ground truth.
The accuracy of the camera's measurements is verified by a series of physically measured positions. The deviation of these values from the camera measurement was less than the resolution of the physical measurements (1°) indicating that the visual measurement is consistent with ground truth.
A servo motor is a type of motor that is capable of controlling the angle of rotation and speed based on an external input signal. The current value plays a very important role in the control process of a servo motor. Under normal circumstances, the current value of a servo motor should be positive, but under some special circumstances, the current value may be negative.
Servo motor is a kind of drive device widely used in various industrial automation and intelligent transportation fields. Its working principle is mainly based on the principle of electromagnetic induction, by controlling the speed and steering of the motor in order to achieve precise control. Servo motors have the advantages of high precision, fast response and stability, which make them play a key role in many demanding application scenarios. This article will focus on servo motor current measurement methods to help users better understand and utilize this device.
Correctly measuring the current of servo motors is of great significance for monitoring the operating status of the equipment, early warning of faults and optimized control.
Through the monitoring of the current, we can obtain the real-time load condition of the motor and determine whether its operating status is normal. At the same time, if the current exceeds the rated value, it may lead to overheating or even damage of the servo motor, so the accurate measurement of current is also a key link to prevent equipment failure.

Correctly measuring the current of servo motors is of great significance for monitoring the operating status of the equipment, early warning of faults and optimized control.
Through the monitoring of the current, we can obtain the real-time load condition of the motor and determine whether its operating status is normal. At the same time, if the current exceeds the rated value, it may lead to overheating or even damage of the servo motor, so the accurate measurement of current is also a key link to prevent equipment failure.
Servo motor is a kind of motor commonly used in precision control system, which can precisely control the speed and position of the motor according to the control signal. When installing and using a servo motor, disconnecting or wiring is a very important step, which directly affects the working effect and safety of the motor.
Servo motors are high-precision, high-performance motors that are widely used in robotics, automation equipment, CNC machine tools, and other fields. The optimum speed range of a servo motor is related to the structure of the motor, the control system, load characteristics and other factors. Generally speaking, the optimal speed range of the servo motor is near the rated speed of the motor, usually between 70% and 120% of the rated speed. In this range, the output power and efficiency of the motor are the highest, and the stability and precision of the motor can also be ensured.
The response speed of the servo motor is the delay time from the input control signal to the actual movement of the motor, that is, the degree of speed of the motor response. If the response speed of the servo motor is slow, it will lead to a decline in the performance of the control system and will not be able to meet the requirements of the actual application. So, what are the reasons for the slow response of the servo motor?
A servo motor is a type of rotary or linear actuator that allows for precise control of angular or linear position, velocity, and acceleration. Selecting the right servo motor can be a challenging task, and finding a motor that meets your speed, torque, and power requirements is not enough. There are many factors to consider when selecting a motor that meets your application requirements.
We will provide you with some checks to prevent motor overheating and save you time and money on motor replacement. If you are currently experiencing motor overheating problems, we hope this article will help you determine the cause.

We will provide you with some checks to prevent motor overheating and save you time and money on motor replacement. If you are currently experiencing motor overheating problems, we hope this article will help you determine the cause.
Motor too small for use; high ambient temperature; continuous operation intermittent load motor; high-voltage or low-voltage power supply; high altitude; ventilation holes blocked are the 6 reasons why industrial servo motors overheat.
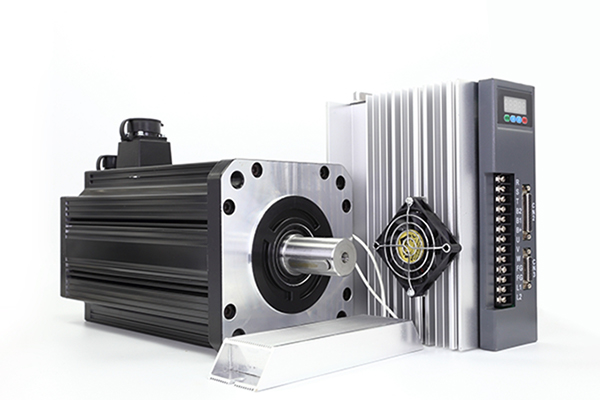
Category
Featured Articles
What is a Servo Motor?
There are some special types of application of electrical motor where rotation of the motor is required for just a certain angle ...
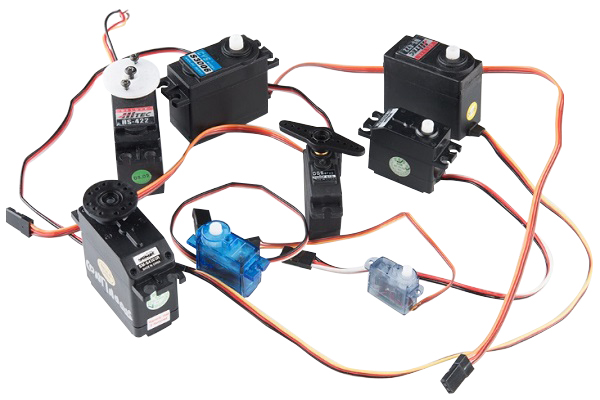
How to Test Servo Motor?
Servo motors are devices that convert electrical signals into mechanical motion and are widely used in industrial automation, ...

What are the Types of Servo Motor?
There are some special types of application of electrical motor where rotation of the motor is required for just a certain angle ...

How to Maintain Servo Motor?
Servo motors play a crucial role in various industries, serving as precision control devices in applications ranging from ...

How to Select the Suitable Power ...
It's important to consider the unique demands of a motion control application when selecting a power supply. During ...
