Home » Servo System » What is Servo System?
What is Servo System?
A feedback control system used to precisely follow or reproduce a process. Also known as a follower system. In many cases, a servo system refers exclusively to a feedback control system in which the controlled quantity (the output of the system) is a mechanical displacement or displacement velocity or acceleration, and its function is to make the output mechanical displacement (or angle of rotation) accurately follow the input displacement (or angle of rotation). There is no principle difference between the structural composition of a servo system and other forms of feedback control systems.
Servo system was firstly used in ship's autopilot, artillery control and command instrument, and then gradually spread to many fields, especially automatic lathe, antenna position control, missile and spacecraft guidance, etc.. The use of servo systems is mainly to achieve the following purposes:
Therefore, high-precision measuring elements must be used in servo systems, such as precision potentiometers, self-rectifiers, resolvers, optical encoders, optical encoders, magnetic grids and ball grids. In addition, additional measures can be taken to improve the accuracy of the system, for example, the measuring element (such as self-rectifying machine) of the measuring axis through the reducer connected to the rotary axis, so that the rotary angle of the rotary axis has been amplified to improve the relative measurement accuracy. Servo systems using this scheme are called fine-measurement coarse-measurement systems or dual-channel systems. The goniometric line that engages the rotary axis through the gearbox is called the fine reading channel, and the goniometric line taken directly from the rotary axis is called the coarse reading channel.
Tendency of Application
Automatic control system is not only in the theory of rapid development, in its application of the device is also rapidly changing. Modular, digital, high-precision, long-life devices every 3 to 5 years, there are newer products on the market. The traditional AC servo motor characteristics of soft, and its output characteristics are not single-valued; stepper motor is generally open-loop control and can not be accurately positioned, the motor itself has a speed resonance zone, pwm speed control system for position tracking performance is poor, frequency control is simple but sometimes not enough precision.
DC motor servo system is widely used in position follower system with its excellent performance, but it also has disadvantages, such as complex structure, prominent dead zone contradiction at ultra-low speed, and commutation brush will bring noise and maintenance problems. At present, the new permanent magnet AC servo motor is developing rapidly, especially from square wave control to sinusoidal wave control, the system performance is better.

Servo system was firstly used in ship's autopilot, artillery control and command instrument, and then gradually spread to many fields, especially automatic lathe, antenna position control, missile and spacecraft guidance, etc.. The use of servo systems is mainly to achieve the following purposes:
- Small power command signal to control high-power loads. Artillery control and rudder control are typical examples.
- In the absence of mechanical connection, the input shaft controls the output shaft located at a distance, realizing long-distance synchronous transmission.
- To make output mechanical displacements accurately track electrical signals, such as recording and indicating instruments.
Therefore, high-precision measuring elements must be used in servo systems, such as precision potentiometers, self-rectifiers, resolvers, optical encoders, optical encoders, magnetic grids and ball grids. In addition, additional measures can be taken to improve the accuracy of the system, for example, the measuring element (such as self-rectifying machine) of the measuring axis through the reducer connected to the rotary axis, so that the rotary angle of the rotary axis has been amplified to improve the relative measurement accuracy. Servo systems using this scheme are called fine-measurement coarse-measurement systems or dual-channel systems. The goniometric line that engages the rotary axis through the gearbox is called the fine reading channel, and the goniometric line taken directly from the rotary axis is called the coarse reading channel.
Tendency of Application
Automatic control system is not only in the theory of rapid development, in its application of the device is also rapidly changing. Modular, digital, high-precision, long-life devices every 3 to 5 years, there are newer products on the market. The traditional AC servo motor characteristics of soft, and its output characteristics are not single-valued; stepper motor is generally open-loop control and can not be accurately positioned, the motor itself has a speed resonance zone, pwm speed control system for position tracking performance is poor, frequency control is simple but sometimes not enough precision.
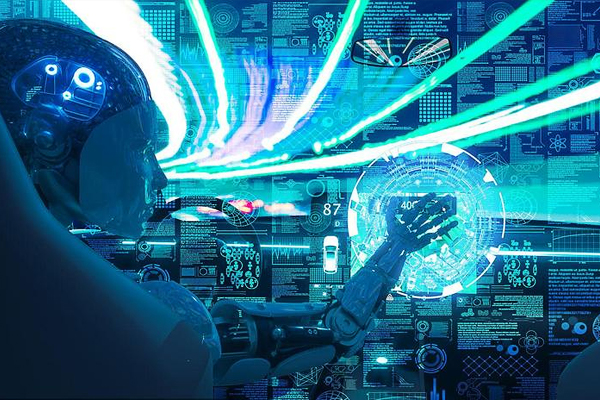
DC motor servo system is widely used in position follower system with its excellent performance, but it also has disadvantages, such as complex structure, prominent dead zone contradiction at ultra-low speed, and commutation brush will bring noise and maintenance problems. At present, the new permanent magnet AC servo motor is developing rapidly, especially from square wave control to sinusoidal wave control, the system performance is better.
Post a Comment:
You may also like:
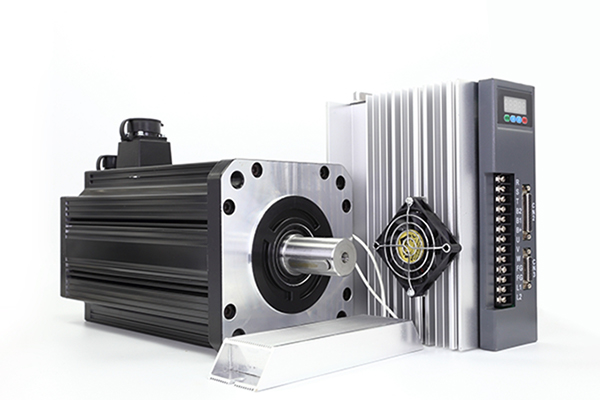
Category
Featured Articles
What are the Basic Components of ...
Servomechanisms, called servos for short, are the basic building blocks of power drives. In this manual what we mean by a power ...

What is the Bandwidth of ...
For a servo system, the bandwidth is the maximum sine wave frequency to which the servo system can respond. In professional ...

What Should Consider Before Using ...
Servo system is a commonly used control system, widely used in industrial automation. It compares the output signal with the ...
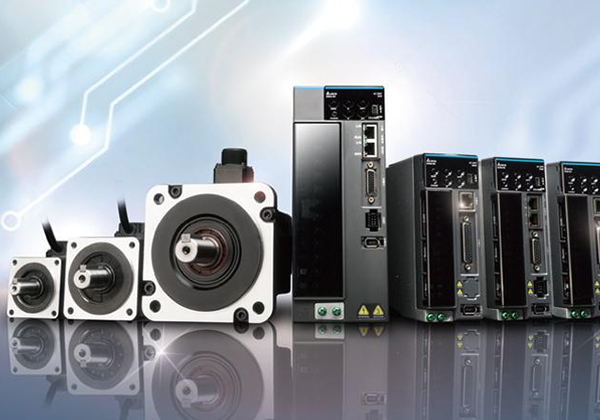
What is Servo System?
A feedback control system used to precisely follow or reproduce a process. Also known as a follower system. In many cases, a ...
