What is Positioning Principle in Servo Motor?
A servo motor is a type of motor that can realize precise position control based on input control signals. It can precisely control the position of the motor by controlling the motor's speed and steering so that it stops at the specified position. The positioning principle of a servo motor involves several important technical points, which will be introduced one by one in this article.
The positioning principle of servo motors is closely related to encoders. An encoder is a device that can convert the angle of rotation or displacement into an electrical signal output. In servo motors, an incremental encoder is usually used. Incremental encoders represent the angle or displacement of each revolution by a fixed number of pulses. By counting and decoding the number of pulses output by the encoder, precise measurement and control of the motor position can be realized.
The positioning principle of the servo motor involves a closed-loop control system. A closed-loop control system is a control system based on the principle of feedback, which realizes closed-loop control of position by comparing the position information output from the motor with the desired position, calculating the error and adjusting the control signal according to the error value. The closed-loop control system of a servo motor usually consists of a position sensor, a controller and a power amplifier. The position sensor is used to measure the position of the motor, the controller calculates the control signal based on the position error, and the power amplifier converts the control signal into a motor drive signal to drive the motor to rotate to the desired position.
PID control algorithm is a commonly used control method, which regulates the control signal through proportional, integral and differential to make the system response more stable and precise. In servo motors, PID control algorithms are commonly used in controllers to calculate control signals based on the magnitude of the error value and the rate of change. The proportional term is used to control the sensitivity of the response, the integral term is used to eliminate the steady state error, and the differential term is used to suppress overshooting and improve the response speed of the system.
The positioning principle of servo motor also involves the stability analysis of the feedback control system. Stability is a very important index in the control system, which determines whether the system can work stably. In servo motors, stability analysis is usually carried out through the frequency domain method and the time domain method. The frequency domain method is mainly used to analyze the frequency response and stability boundaries of the system by plotting Bode and Nyquist diagrams. The time domain method is mainly used to analyze the time response and stability characteristics of the system by plotting the step response and shock response.
The positioning principle of a servo motor is based on encoder position measurement and closed-loop control. It realizes precise control of the motor position by using PID control algorithms and stability analysis methods. Servo motors are widely used in a variety of automation equipment and mechanical systems, such as industrial machinery, robots, and medical equipment. Through continuous innovation and improvement, the positioning accuracy and control performance of servo motors will be further improved to provide stronger power support for modern industrial production and scientific research.
The positioning principle of servo motors is closely related to encoders. An encoder is a device that can convert the angle of rotation or displacement into an electrical signal output. In servo motors, an incremental encoder is usually used. Incremental encoders represent the angle or displacement of each revolution by a fixed number of pulses. By counting and decoding the number of pulses output by the encoder, precise measurement and control of the motor position can be realized.
The positioning principle of the servo motor involves a closed-loop control system. A closed-loop control system is a control system based on the principle of feedback, which realizes closed-loop control of position by comparing the position information output from the motor with the desired position, calculating the error and adjusting the control signal according to the error value. The closed-loop control system of a servo motor usually consists of a position sensor, a controller and a power amplifier. The position sensor is used to measure the position of the motor, the controller calculates the control signal based on the position error, and the power amplifier converts the control signal into a motor drive signal to drive the motor to rotate to the desired position.
PID control algorithm is a commonly used control method, which regulates the control signal through proportional, integral and differential to make the system response more stable and precise. In servo motors, PID control algorithms are commonly used in controllers to calculate control signals based on the magnitude of the error value and the rate of change. The proportional term is used to control the sensitivity of the response, the integral term is used to eliminate the steady state error, and the differential term is used to suppress overshooting and improve the response speed of the system.
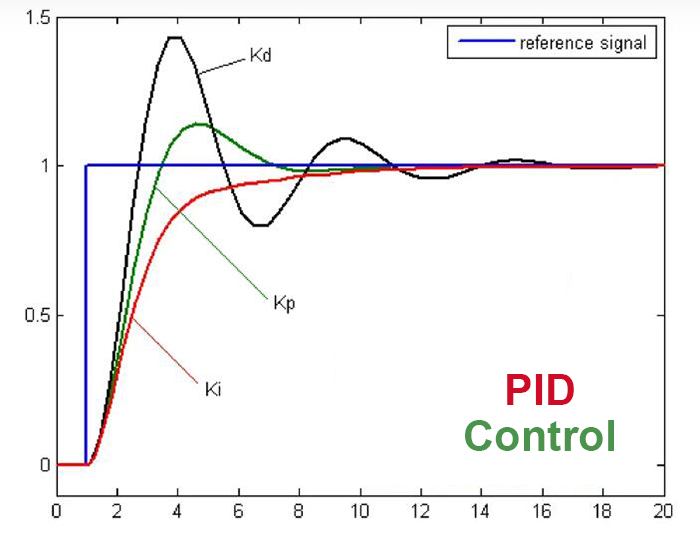

Post a Comment:
You may also like:
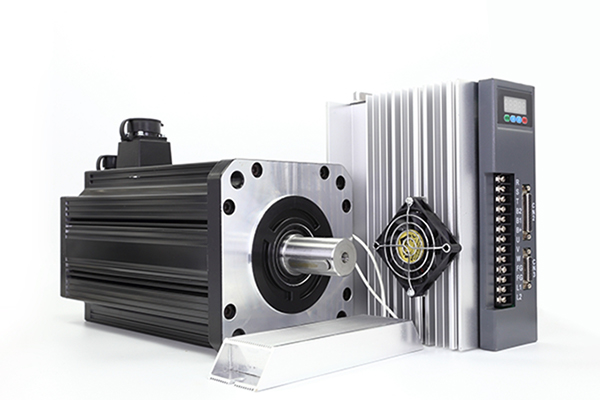
Category
Featured Articles
Troubleshooting of Servo Motor
Servo motors play a crucial role in various industrial applications, providing precision control and efficient performance. ...

Safety Precaution For Using Servo Motor
In the realm of industrial automation, servo motors play a crucial role in achieving precision and control. These devices are ...

Why Use Servo Motor as Test Load?
Dynamometer is mainly divided into two parts: cabinet and frame, while the frame mainly has the motor under test, torque speed ...
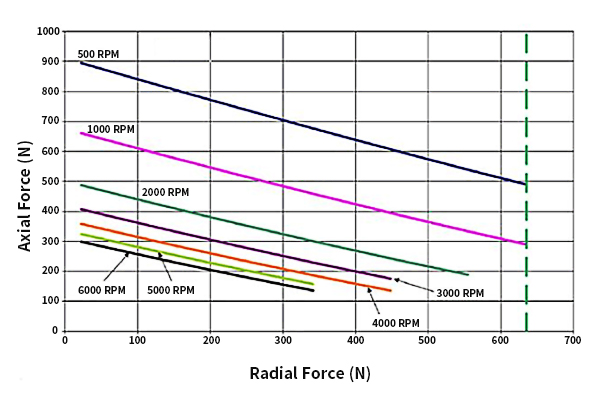
Difference Between Servo and Stepper ...
Servo motor and stepper motor are almost used in all automated industries where high precision is to be achieved. Though servo ...
