What are the Steps in Designing a Servo Motor?
Servo motor is a kind of motor that can precisely control the speed and position, which is widely used in the field of mechanical equipment and industrial automation. The design process of servo motor needs to go through several steps, this article will introduce the specific steps of servo motor design in detail.
Step 1: Determine requirements and specifications
Before designing the servo motor, it is first necessary to clarify the use requirements and specifications of the motor. Including motor rated power, rated speed, rated torque, power supply voltage and other parameters. At the same time, it is also necessary to determine the working environment and special requirements of the motor according to the specific application scenario, such as temperature, humidity, protection level, etc.
Step 2: Select motor type
After determining the requirements and specifications, you need to choose the right type of servo motor according to the specific situation. Common servo motor types include DC servo motors, AC servo motors and stepper servo motors. According to different application scenarios, choosing the right type of motor is the key to ensure the performance and stability of the motor.
Step 3: Calculate load characteristics
When designing a servo motor, you need to calculate the load characteristics, including load inertia, load torque and load inertia ratio. The calculation of load characteristics is to determine the performance index of the motor and the parameters of the control system in order to realize a good control effect.
Step 4: Selecting a reducer
In order to meet the requirements of the load, it is often necessary to install a gearhead on the servo motor. A speed reducer reduces the speed of the motor and increases the output torque. Choosing the right gearhead requires consideration of parameters such as the load's rotational speed, torque and reduction ratio.
Step 5: Choose a drive
The drive is an important part of the servo motor, which controls the speed and position of the motor. Select the appropriate drive according to the motor type and requirements, such as DC drive, AC drive or stepper drive. Driver selection should consider factors such as the motor's rated parameters, control mode and interface.
Step 6: Design the control system
The control system of a servo motor consists of a controller and a feedback device. The controller is responsible for receiving input signals, calculating output control signals, and sending them to the driver. The feedback device is used to monitor the speed and position of the motor in real time and send the feedback signal to the controller. Designing the control system requires consideration of factors such as the controller's control algorithm, sampling period and stability.
Step 7: Perform simulation and optimization
After the design is completed, simulation software can be used to simulate and optimize the servo motor. Simulation allows you to evaluate the performance and stability of the motor and make parameter adjustments and optimization. The goal of optimization is to improve the response speed, control accuracy and anti-interference ability of the motor.
Step 8: Manufacturing and testing
After design and optimization are complete, manufacturing of the servo motor can begin. The manufacturing process includes shopping for parts, assembling the motor and debugging the control system. After manufacturing is completed, rigorous testing and verification is required to ensure that the performance and stability of the motor meets the design requirements.
Step 9: Installation and commissioning
When installing the servo motor, it needs to be arranged and connected according to the specific application scenario. At the same time, debugging and optimization are also needed to adjust the control parameters and feedback devices according to the actual situation. The debugging process needs to pay attention to safety and accuracy to ensure the normal operation and stability of the motor.
Step 10: Maintenance and monitoring
Maintenance and monitoring of the servo motor is the key to ensure its long-term stable operation. Regularly check and clean the motor and replace worn parts in time. At the same time, monitoring equipment and software can be used to monitor and analyze the running status of the motor in real time, so as to find and solve problems in time.
Through the above ten steps, the design process of servo motor can be completed. Designing a servo motor with stable performance and precise control requires comprehensive consideration of several factors, including demand specifications, load characteristics, drive selection, and control system design. Only through careful analysis and optimization in each step can we design a high precision servo motor that meets the actual demand.
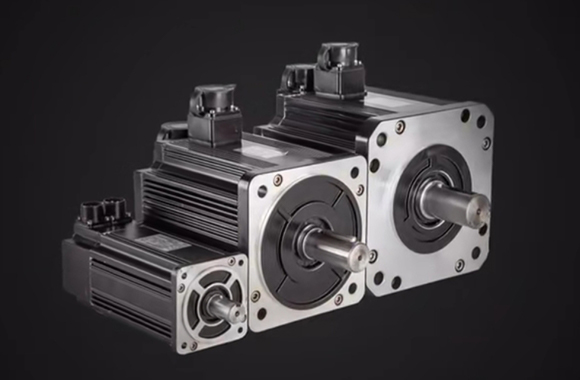
Step 1: Determine requirements and specifications
Before designing the servo motor, it is first necessary to clarify the use requirements and specifications of the motor. Including motor rated power, rated speed, rated torque, power supply voltage and other parameters. At the same time, it is also necessary to determine the working environment and special requirements of the motor according to the specific application scenario, such as temperature, humidity, protection level, etc.
Step 2: Select motor type
After determining the requirements and specifications, you need to choose the right type of servo motor according to the specific situation. Common servo motor types include DC servo motors, AC servo motors and stepper servo motors. According to different application scenarios, choosing the right type of motor is the key to ensure the performance and stability of the motor.
Step 3: Calculate load characteristics
When designing a servo motor, you need to calculate the load characteristics, including load inertia, load torque and load inertia ratio. The calculation of load characteristics is to determine the performance index of the motor and the parameters of the control system in order to realize a good control effect.
Step 4: Selecting a reducer
In order to meet the requirements of the load, it is often necessary to install a gearhead on the servo motor. A speed reducer reduces the speed of the motor and increases the output torque. Choosing the right gearhead requires consideration of parameters such as the load's rotational speed, torque and reduction ratio.
Step 5: Choose a drive
The drive is an important part of the servo motor, which controls the speed and position of the motor. Select the appropriate drive according to the motor type and requirements, such as DC drive, AC drive or stepper drive. Driver selection should consider factors such as the motor's rated parameters, control mode and interface.
Step 6: Design the control system
The control system of a servo motor consists of a controller and a feedback device. The controller is responsible for receiving input signals, calculating output control signals, and sending them to the driver. The feedback device is used to monitor the speed and position of the motor in real time and send the feedback signal to the controller. Designing the control system requires consideration of factors such as the controller's control algorithm, sampling period and stability.
Step 7: Perform simulation and optimization
After the design is completed, simulation software can be used to simulate and optimize the servo motor. Simulation allows you to evaluate the performance and stability of the motor and make parameter adjustments and optimization. The goal of optimization is to improve the response speed, control accuracy and anti-interference ability of the motor.
Step 8: Manufacturing and testing
After design and optimization are complete, manufacturing of the servo motor can begin. The manufacturing process includes shopping for parts, assembling the motor and debugging the control system. After manufacturing is completed, rigorous testing and verification is required to ensure that the performance and stability of the motor meets the design requirements.
Step 9: Installation and commissioning
When installing the servo motor, it needs to be arranged and connected according to the specific application scenario. At the same time, debugging and optimization are also needed to adjust the control parameters and feedback devices according to the actual situation. The debugging process needs to pay attention to safety and accuracy to ensure the normal operation and stability of the motor.
Step 10: Maintenance and monitoring
Maintenance and monitoring of the servo motor is the key to ensure its long-term stable operation. Regularly check and clean the motor and replace worn parts in time. At the same time, monitoring equipment and software can be used to monitor and analyze the running status of the motor in real time, so as to find and solve problems in time.
Through the above ten steps, the design process of servo motor can be completed. Designing a servo motor with stable performance and precise control requires comprehensive consideration of several factors, including demand specifications, load characteristics, drive selection, and control system design. Only through careful analysis and optimization in each step can we design a high precision servo motor that meets the actual demand.
Post a Comment:
You may also like:
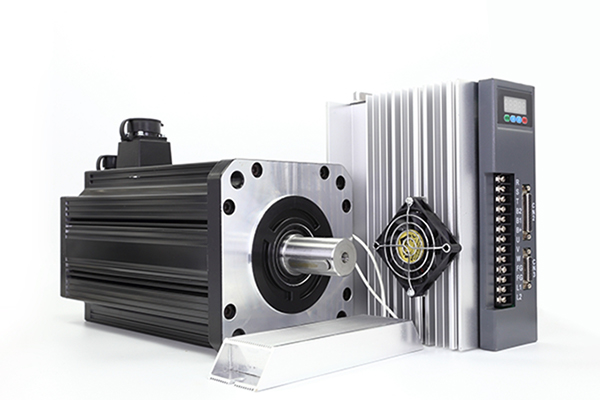
Category
Featured Articles
Troubleshooting of Servo Motor
Servo motors play a crucial role in various industrial applications, providing precision control and efficient performance. ...

Safety Precaution For Using Servo Motor
In the realm of industrial automation, servo motors play a crucial role in achieving precision and control. These devices are ...

Why Use Servo Motor as Test Load?
Dynamometer is mainly divided into two parts: cabinet and frame, while the frame mainly has the motor under test, torque speed ...
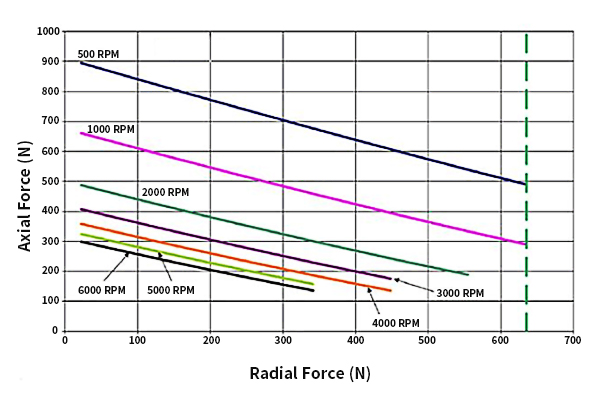
Difference Between Servo and Stepper ...
Servo motor and stepper motor are almost used in all automated industries where high precision is to be achieved. Though servo ...
