What are the Driving Modes of Servo Motor?
Servo motor is a kind of motor that can realize precise control and position feedback, and its transmission mode plays a crucial role in the performance and application scenario of the motor. In this paper, we will discuss the principle, characteristics and application of servo motor transmission mode from the perspective of its transmission mode.
Principle of Servo Motor Drive Mode
The drive mode of servo motor mainly includes direct drive and indirect drive. Direct drive means that the rotor of the motor is directly connected to the load, and the load is driven by the rotation of the motor itself. Indirect drive, on the other hand, transmits the motion of the motor to the load through transmission devices, such as gears and belts.
The two most common types of direct drive methods are linear drive and rotary drive. Linear drive means that the rotor of the motor is aligned with the axis of linear movement of the load, such as linear motors. Rotary drive means that the rotor of the motor is aligned with the axis of rotation of the load, such as rotary motors.
Common transmissions in indirect drive methods are gear drives, belt drives and screw drives. Gear drive is to transfer the rotation of the motor to the load through the meshing of the gears, suitable for scenes that require large torque and precise transmission. Belt drive transmits the rotation of the motor to the load through the belt, which is suitable for the scenario of larger transmission ratio and higher vibration damping requirements. Screw drive is to convert the rotation of the motor into linear motion by means of a screw, which is suitable for the scenarios that require precise control of the position.
Type of Servo Motor Drive Mode
The direct drive method is characterized by simple structure, fast response speed and high accuracy. Linear drive can realize high-speed, high-precision linear motion, suitable for scenes that require fast and accurate positioning, such as CNC machine tools, semiconductor equipment, etc. Rotary drive can realize high-speed, high-precision rotary motion, suitable for scenes requiring fast and accurate rotation, such as robotic arms, aerospace equipment and so on.

The indirect drive method is characterized by large transmission ratio and high torque. Gear drive can realize high torque output and precise transmission, suitable for scenes requiring high torque and high transmission precision, such as construction machinery, lifting equipment and so on. Belt drive can realize a large transmission ratio and good vibration damping, suitable for scenes requiring a large transmission ratio and high vibration damping requirements, such as wind turbines, conveying equipment, and so on. Screw drive can realize linear motion and precise position control, suitable for scenes that require precise positioning, such as printing equipment, medical equipment, etc.
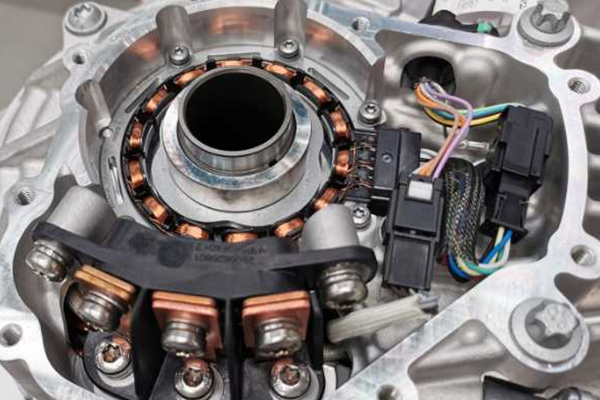
Servo motors in direct drive mode are often used in scenarios that require high-speed, high-precision movements. For example, in CNC machine tools, linear drive servo motors can realize fast and accurate positioning and machining. In robot arms, rotary-driven servo motors can realize fast and accurate gripping and placing.
Servo motors with indirect drive mode are often used in scenarios that require high torque and high transmission accuracy. For example, in engineering machinery, gear-driven servo motors can realize high torque output and accurate transmission. In wind turbines, belt-driven servo motors can realize large transmission ratios and good vibration damping.
Servomotors with helical drives are often used in scenarios where precise position control is required. For example, in printing equipment, screw-driven servomotors can realize precise printing position control. In medical equipment, screw-driven servomotors can realize precise position adjustment and operation.
The selection of servo motor transmission mode should be determined according to the specific application requirements. Different transmission methods have different characteristics and applicable scenarios, and a reasonable choice of transmission methods can improve the performance and application effect of servo motors. Through continuous technological innovation and application research, servo motor transmission mode will be used in more fields, and bring more possibilities for the development of automation equipment.
Principle of Servo Motor Drive Mode
The drive mode of servo motor mainly includes direct drive and indirect drive. Direct drive means that the rotor of the motor is directly connected to the load, and the load is driven by the rotation of the motor itself. Indirect drive, on the other hand, transmits the motion of the motor to the load through transmission devices, such as gears and belts.
The two most common types of direct drive methods are linear drive and rotary drive. Linear drive means that the rotor of the motor is aligned with the axis of linear movement of the load, such as linear motors. Rotary drive means that the rotor of the motor is aligned with the axis of rotation of the load, such as rotary motors.
Common transmissions in indirect drive methods are gear drives, belt drives and screw drives. Gear drive is to transfer the rotation of the motor to the load through the meshing of the gears, suitable for scenes that require large torque and precise transmission. Belt drive transmits the rotation of the motor to the load through the belt, which is suitable for the scenario of larger transmission ratio and higher vibration damping requirements. Screw drive is to convert the rotation of the motor into linear motion by means of a screw, which is suitable for the scenarios that require precise control of the position.
Type of Servo Motor Drive Mode
The direct drive method is characterized by simple structure, fast response speed and high accuracy. Linear drive can realize high-speed, high-precision linear motion, suitable for scenes that require fast and accurate positioning, such as CNC machine tools, semiconductor equipment, etc. Rotary drive can realize high-speed, high-precision rotary motion, suitable for scenes requiring fast and accurate rotation, such as robotic arms, aerospace equipment and so on.

The indirect drive method is characterized by large transmission ratio and high torque. Gear drive can realize high torque output and precise transmission, suitable for scenes requiring high torque and high transmission precision, such as construction machinery, lifting equipment and so on. Belt drive can realize a large transmission ratio and good vibration damping, suitable for scenes requiring a large transmission ratio and high vibration damping requirements, such as wind turbines, conveying equipment, and so on. Screw drive can realize linear motion and precise position control, suitable for scenes that require precise positioning, such as printing equipment, medical equipment, etc.
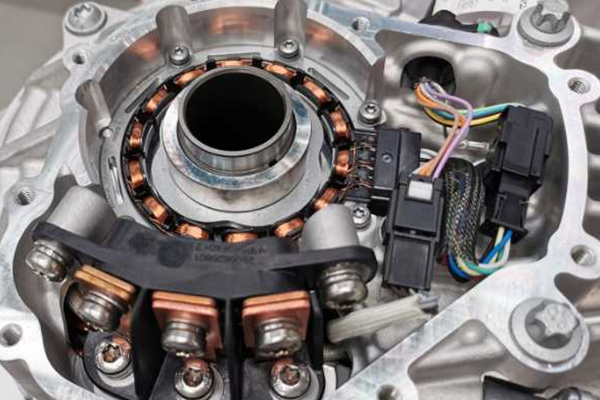
Servo motors in direct drive mode are often used in scenarios that require high-speed, high-precision movements. For example, in CNC machine tools, linear drive servo motors can realize fast and accurate positioning and machining. In robot arms, rotary-driven servo motors can realize fast and accurate gripping and placing.
Servo motors with indirect drive mode are often used in scenarios that require high torque and high transmission accuracy. For example, in engineering machinery, gear-driven servo motors can realize high torque output and accurate transmission. In wind turbines, belt-driven servo motors can realize large transmission ratios and good vibration damping.
Servomotors with helical drives are often used in scenarios where precise position control is required. For example, in printing equipment, screw-driven servomotors can realize precise printing position control. In medical equipment, screw-driven servomotors can realize precise position adjustment and operation.
The selection of servo motor transmission mode should be determined according to the specific application requirements. Different transmission methods have different characteristics and applicable scenarios, and a reasonable choice of transmission methods can improve the performance and application effect of servo motors. Through continuous technological innovation and application research, servo motor transmission mode will be used in more fields, and bring more possibilities for the development of automation equipment.
Post a Comment:
You may also like:
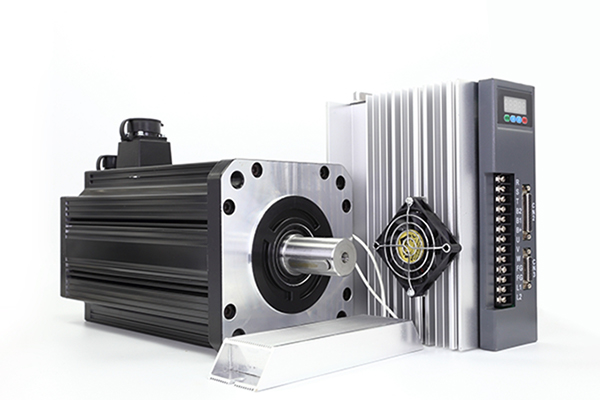
Category
Featured Articles
How to Test Servo Motor?
Servo motors are devices that convert electrical signals into mechanical motion and are widely used in industrial automation, ...

How to Maintain Servo Motor?
Servo motors play a crucial role in various industries, serving as precision control devices in applications ranging from ...

What are the Types of Servo Motor?
There are some special types of application of electrical motor where rotation of the motor is required for just a certain angle ...

How to Select the Suitable Power ...
It's important to consider the unique demands of a motion control application when selecting a power supply. During ...

What is a Servo Motor?
There are some special types of application of electrical motor where rotation of the motor is required for just a certain angle ...
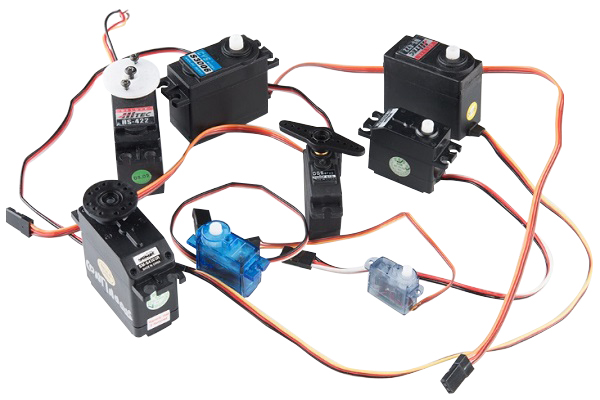