Home » Servo System » What are the Basic Components of Servomechanism?
What are the Basic Components of Servomechanism?
Servomechanisms, called servos for short, are the basic building blocks of power drives. In this manual what we mean by a power drive is an electric or electrohydraulic machine which positions a launcher or other device in accordance with a relatively weak electrical signal. We will consider a power drive as a big servo made up of smaller ones. We will define a servo and talk about its main components.
The figure shows a block diagram of an elementary servo. It consists of two blocks and some connecting lines. If you are not familiar with it already, study the diagram carefully and memorize it. From this simple concept of a servo will spring one of the most important ideas you will ever encounter in your naval career as a technician - the feedback principle. Not only is feedback important in understanding servos, but it also has important applications in the electronic and hydraulic fields. Therefore, if you know how feedback is used in servos, you can better understand how it is used in electronics and hydraulics. At this writing there is no standard definition of a servo. For the purpose of this chapter, we will call a servo any electrical, electronic, mechanical, or hydraulic system which uses feedback. But a rigorous definition is relatively unimportant. What is important is that you know what makes a group of parts a servo. Regardless of their physical form electric, electronic, mechanical, hydraulic, or combinations of these - all servos have the following characteristics.
Control Device
The basic job of the servo is to position a load. The load can be a launcher guide or carriage, a rammer, a hydraulic valve or piston, a dial, an electric motor, a mechanical linkage, etc. The load is attached in some manner to the output of the servo. Consider a launcher guide. Its position is controlled in accordance with launcher train and elevation orders which are inputs to the servo.
Power Amplifier
The input to a servo is usually a very small signal. It is too weak to move the load by itself, so some sort of power amplification must take place within the servo. Again take as an example a servo used to position a launcher guide. The input to the servo is sometimes so small it can be measured with a milliammeter. To develop enough power to move the great weight of a guide arm requires currents in the ampere range. Therefore, every power drive you will work with has one or more amplifying stages in it. The amplifier may be electrical, electronic, hydraulic, or one or more of these types of amplifiers in combination.
Closed Loop System
A servo is called a closed loop system because it uses feedback. Feedback is a principle upon which the operation of all servos is based. You can see that the feedback line runs from the output to the block marked error detector. This feedback is a communication channel which reports the condition (speed, position) of the output back to the error detector. To see how feedback works, assume the input is a mechanical signal telling the output to move to a certain position. If the output is not at the ordered position, the feedback signal reports the position of the output to the error detector. The error detector measures the difference between the ordered position (input) and the actual position of the output. Also, the error detector performs a simple mathematical operation: it subtracts the output from the input to get the amount of difference, or error, as it is called. Thus the error is the actual input to the amplifier, not the quantity marked input. Also notice that when the feedback equals the input, the error signal is zero and no signal is given to the servo. But whenever the feedback differs from the input, an error signal is developed. The error signal drives the output in such a manner as to reduce the error signal. Since the principle of feedback is used in servos, they are often called closed loop systems or servo loops. Keep in mind that feedback can be transmitted electrically, hydraulically, or mechanically in a servo. Feedback is also called response by many technicians. When the feedback line defines the position of the servo's output shaft or its load, the feedback is called position feedback.
Entire System
It cannot consist of a single component. It must have the minimum number of components we have shown in the block diagram in the picture. There is no law against a servo having more sections than the ones we have shown. And they usually do. But regardless of the number of parts in a servo, they all work together as a system or team. And this system concept is important. A servo is not an isolated motor or power amplifier, but must be considered as an entire system of interconnected components. Together, these components measure, transmit, compare, amplify, and control quantities.
The figure shows a block diagram of an elementary servo. It consists of two blocks and some connecting lines. If you are not familiar with it already, study the diagram carefully and memorize it. From this simple concept of a servo will spring one of the most important ideas you will ever encounter in your naval career as a technician - the feedback principle. Not only is feedback important in understanding servos, but it also has important applications in the electronic and hydraulic fields. Therefore, if you know how feedback is used in servos, you can better understand how it is used in electronics and hydraulics. At this writing there is no standard definition of a servo. For the purpose of this chapter, we will call a servo any electrical, electronic, mechanical, or hydraulic system which uses feedback. But a rigorous definition is relatively unimportant. What is important is that you know what makes a group of parts a servo. Regardless of their physical form electric, electronic, mechanical, hydraulic, or combinations of these - all servos have the following characteristics.

The basic job of the servo is to position a load. The load can be a launcher guide or carriage, a rammer, a hydraulic valve or piston, a dial, an electric motor, a mechanical linkage, etc. The load is attached in some manner to the output of the servo. Consider a launcher guide. Its position is controlled in accordance with launcher train and elevation orders which are inputs to the servo.
Power Amplifier
The input to a servo is usually a very small signal. It is too weak to move the load by itself, so some sort of power amplification must take place within the servo. Again take as an example a servo used to position a launcher guide. The input to the servo is sometimes so small it can be measured with a milliammeter. To develop enough power to move the great weight of a guide arm requires currents in the ampere range. Therefore, every power drive you will work with has one or more amplifying stages in it. The amplifier may be electrical, electronic, hydraulic, or one or more of these types of amplifiers in combination.
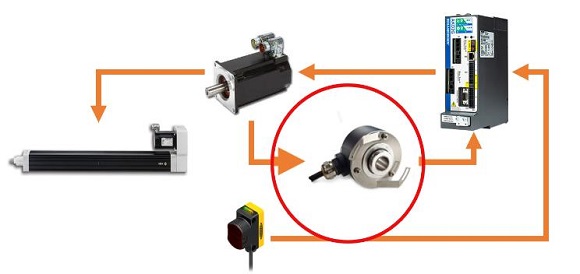
A servo is called a closed loop system because it uses feedback. Feedback is a principle upon which the operation of all servos is based. You can see that the feedback line runs from the output to the block marked error detector. This feedback is a communication channel which reports the condition (speed, position) of the output back to the error detector. To see how feedback works, assume the input is a mechanical signal telling the output to move to a certain position. If the output is not at the ordered position, the feedback signal reports the position of the output to the error detector. The error detector measures the difference between the ordered position (input) and the actual position of the output. Also, the error detector performs a simple mathematical operation: it subtracts the output from the input to get the amount of difference, or error, as it is called. Thus the error is the actual input to the amplifier, not the quantity marked input. Also notice that when the feedback equals the input, the error signal is zero and no signal is given to the servo. But whenever the feedback differs from the input, an error signal is developed. The error signal drives the output in such a manner as to reduce the error signal. Since the principle of feedback is used in servos, they are often called closed loop systems or servo loops. Keep in mind that feedback can be transmitted electrically, hydraulically, or mechanically in a servo. Feedback is also called response by many technicians. When the feedback line defines the position of the servo's output shaft or its load, the feedback is called position feedback.
Entire System
It cannot consist of a single component. It must have the minimum number of components we have shown in the block diagram in the picture. There is no law against a servo having more sections than the ones we have shown. And they usually do. But regardless of the number of parts in a servo, they all work together as a system or team. And this system concept is important. A servo is not an isolated motor or power amplifier, but must be considered as an entire system of interconnected components. Together, these components measure, transmit, compare, amplify, and control quantities.
Post a Comment:
You may also like:
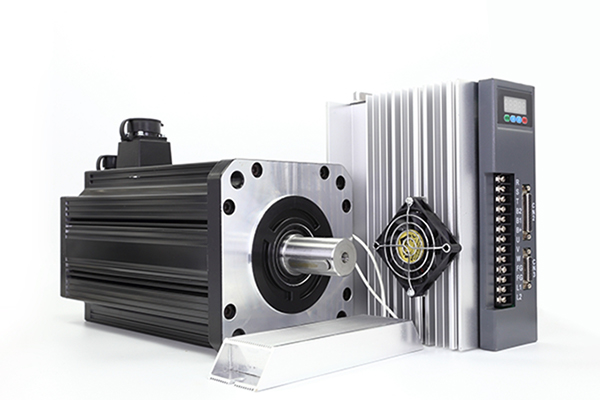
Category
Featured Articles
What is Servo System?
A feedback control system used to precisely follow or reproduce a process. Also known as a follower system. In many cases, a ...

What Should Consider Before Using ...
Servo system is a commonly used control system, widely used in industrial automation. It compares the output signal with the ...
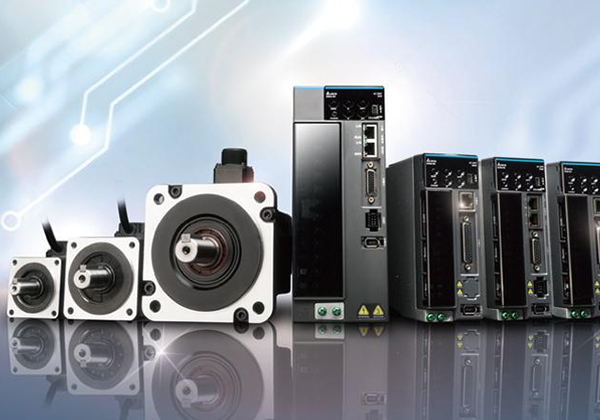
What is the Bandwidth of ...
For a servo system, the bandwidth is the maximum sine wave frequency to which the servo system can respond. In professional ...

What are the Basic Components of ...
Servomechanisms, called servos for short, are the basic building blocks of power drives. In this manual what we mean by a power ...
