Troubleshooting of Servo Motor
Servo motors play a crucial role in various industrial applications, providing precision control and efficient performance. However, like any mechanical or electrical component, servo motors are susceptible to issues that can disrupt their operation. In this article, we will explore common troubleshooting techniques to identify and resolve problems encountered with servo motors.
1. Problems with the braking mechanism:
The servo motor brake is used to brake the motor shaft against rotation when the power is turned off. When the brake is energized, the brake is in the released state. This results in a strange noise, failure to release, and failure to brake.

Solution: The intrusion of foreign objects is a common cause of brake rattling. Secondly, forced operation of the brake in a de-energized state due to a fault in the brake drive circuit can also lead to brake damage.
2. Problems with the cooling unit:
Most small and medium power servo motors are self-cooled. For larger power or special application servo motors, air or liquid cooling is also common. As a result, fan shaking or blocked rotation, coolant leakage.

The culprit for most fan failures is dust. This is because dust accumulates on the blades of the fan over time. The increased load on the blades can lead to vibration and subsequent damage. And with most coolant leaks occurring at the connections, seal failure is usually the problem. Physical damage caused by accidental impact.
Solution: Add filters to fans and replace them regularly; check cooling units regularly.
3. Bearing failure:
As the most important wear parts in the servo motor, more than half of the servo motor failure is usually attributed to bearing problems. Its specific performance is varied, light motor rotation produce shaking, noise, etc., or lead to motor shaft jamming. It is worth noting that bearing failure, if not dealt with in a timely manner, usually also bring secondary damage. For example, bearing corrosion debris flying into the brake or motor encoder, resulting in more serious damage.
Improper mechanical loads (e.g., overload, radial misalignment, axial thrust, belt tension problems); excessive vibration and shock; over-speed operation; moisture or fluid ingress can cause this problem.
Solution: When the servo motor is used, it can not run beyond the rated load for a long time. For occasions with shaft current, add conductive brushes or use motors with insulated bearings for preventive maintenance of the servo motor.
4. Encoder electrical failure:
For encoders with battery back-up, the battery status should be checked first as the battery may be depleted during use and the zero position may be lost. Long-term motor shaft currents may not only affect the motor bearings, but also jeopardize the encoder's built-in bearings, causing burns and damage to the encoder bearings. In addition to incorrect wiring of the encoder, the problem of electromagnetic interference caused by inappropriate wiring is one of the main causes of electrical failure of the encoder.
Solution: Depending on the specific application environment, batteries typically have a life of one or several years. Replacing the batteries at regular intervals reduces the risk of such accidents. Alternatively, a more permanent solution is to switch to a mechanical multi-turn absolute encoder. The motor must be mounted with a reliable earth connection. For cases with shaft currents, the use of insulated bearings and insulated encoders or the addition of a motor shaft grounding device need to be considered.
During the installation of the servo motor, e.g. when adding pulleys or couplings, if knocking is unavoidable, consider removing the encoder for safekeeping and then installing the encoder after all the mechanical installation is complete. In that case, the phase angle of the encoder needs to be readjusted in the servo drive.
Effectively troubleshooting servo motor issues requires a systematic approach, combining a deep understanding of the motor's operation with practical diagnostic techniques.
1. Problems with the braking mechanism:
The servo motor brake is used to brake the motor shaft against rotation when the power is turned off. When the brake is energized, the brake is in the released state. This results in a strange noise, failure to release, and failure to brake.

2. Problems with the cooling unit:
Most small and medium power servo motors are self-cooled. For larger power or special application servo motors, air or liquid cooling is also common. As a result, fan shaking or blocked rotation, coolant leakage.

The culprit for most fan failures is dust. This is because dust accumulates on the blades of the fan over time. The increased load on the blades can lead to vibration and subsequent damage. And with most coolant leaks occurring at the connections, seal failure is usually the problem. Physical damage caused by accidental impact.
Solution: Add filters to fans and replace them regularly; check cooling units regularly.
3. Bearing failure:
As the most important wear parts in the servo motor, more than half of the servo motor failure is usually attributed to bearing problems. Its specific performance is varied, light motor rotation produce shaking, noise, etc., or lead to motor shaft jamming. It is worth noting that bearing failure, if not dealt with in a timely manner, usually also bring secondary damage. For example, bearing corrosion debris flying into the brake or motor encoder, resulting in more serious damage.

Improper mechanical loads (e.g., overload, radial misalignment, axial thrust, belt tension problems); excessive vibration and shock; over-speed operation; moisture or fluid ingress can cause this problem.
Solution: When the servo motor is used, it can not run beyond the rated load for a long time. For occasions with shaft current, add conductive brushes or use motors with insulated bearings for preventive maintenance of the servo motor.
4. Encoder electrical failure:
For encoders with battery back-up, the battery status should be checked first as the battery may be depleted during use and the zero position may be lost. Long-term motor shaft currents may not only affect the motor bearings, but also jeopardize the encoder's built-in bearings, causing burns and damage to the encoder bearings. In addition to incorrect wiring of the encoder, the problem of electromagnetic interference caused by inappropriate wiring is one of the main causes of electrical failure of the encoder.
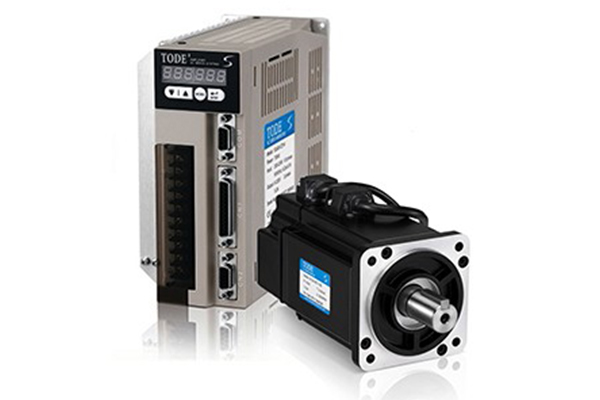
During the installation of the servo motor, e.g. when adding pulleys or couplings, if knocking is unavoidable, consider removing the encoder for safekeeping and then installing the encoder after all the mechanical installation is complete. In that case, the phase angle of the encoder needs to be readjusted in the servo drive.
Effectively troubleshooting servo motor issues requires a systematic approach, combining a deep understanding of the motor's operation with practical diagnostic techniques.
Post a Comment:
You may also like:
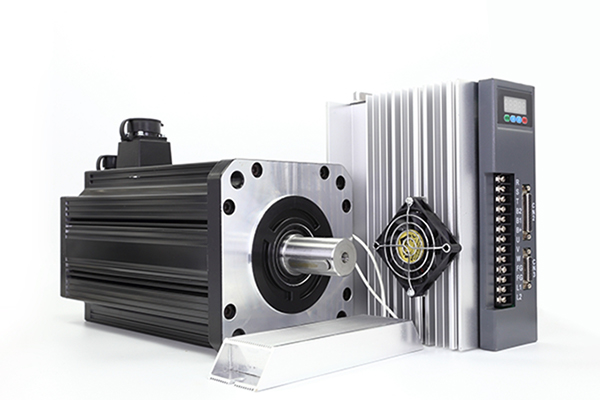
Category
Featured Articles
Difference Between Servo and Stepper ...
Servo motor and stepper motor are almost used in all automated industries where high precision is to be achieved. Though servo ...

Why Use Servo Motor as Test Load?
Dynamometer is mainly divided into two parts: cabinet and frame, while the frame mainly has the motor under test, torque speed ...
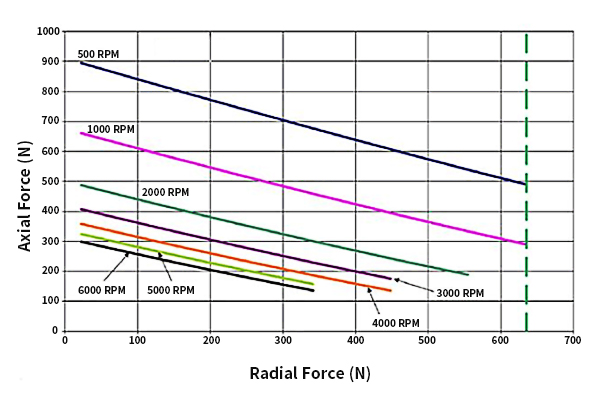
Safety Precaution For Using Servo Motor
In the realm of industrial automation, servo motors play a crucial role in achieving precision and control. These devices are ...

Troubleshooting of Servo Motor
Servo motors play a crucial role in various industrial applications, providing precision control and efficient performance. ...
