Home » Application » Servo System in CNC Machine Tools
Servo System in CNC Machine Tools
As the actuator of CNC machine tools, servo system integrates power electronics, control, drive and protection, and with the progress of digital pulse width modulation technology, special motor material technology, microelectronics technology and modern control technology, it has experienced the development course from stepping to DC and then to AC. There are many kinds of servo systems in CNC machine tools.
Servo system is an electrical transmission automatic control system composed under the guidance of automatic control theory with a motor as the driving device of mechanical motion as the control object, a controller as the core, and a power electronic power conversion device as the actuator. This kind of system controls the torque, speed and angle of the motor, converts electric energy into mechanical energy, and realizes the movement requirements of the machinery.
CNC machine tools, servo system to receive CNC system issued by the displacement, speed commands, through the transformation, amplification and rectification of large, by the motor and mechanical transmission mechanism to drive the machine tool coordinate axis, spindle, etc., driven by the table and the tool holder, through the axis of the linkage so that the tool relative to the workpiece produces a variety of complex mechanical movement, so as to process the user's requirements of complex shapes of the workpiece.
Servo system is an important part of CNC machine tools, CNC machine tools, such as precision and speed indicators are often intended by the servo system. Servo system has undergone the progress from stepping servo to DC servo and then to the communication servo process. And with the progress of technology, high-speed and high-precision processing of linear drive has become a new trend in the progress of the servo system. CNC machine tools on the servo system requirements may be as follows:
Servo system is an electrical transmission automatic control system composed under the guidance of automatic control theory with a motor as the driving device of mechanical motion as the control object, a controller as the core, and a power electronic power conversion device as the actuator. This kind of system controls the torque, speed and angle of the motor, converts electric energy into mechanical energy, and realizes the movement requirements of the machinery.
CNC machine tools, servo system to receive CNC system issued by the displacement, speed commands, through the transformation, amplification and rectification of large, by the motor and mechanical transmission mechanism to drive the machine tool coordinate axis, spindle, etc., driven by the table and the tool holder, through the axis of the linkage so that the tool relative to the workpiece produces a variety of complex mechanical movement, so as to process the user's requirements of complex shapes of the workpiece.
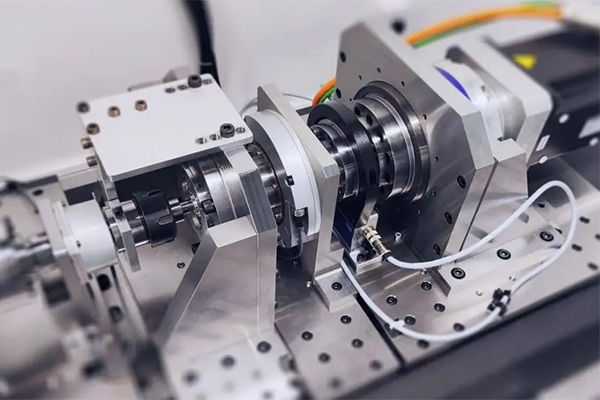
Servo system is an important part of CNC machine tools, CNC machine tools, such as precision and speed indicators are often intended by the servo system. Servo system has undergone the progress from stepping servo to DC servo and then to the communication servo process. And with the progress of technology, high-speed and high-precision processing of linear drive has become a new trend in the progress of the servo system. CNC machine tools on the servo system requirements may be as follows:
- Stability. Stability means that the system can reach a new or return to the original equilibrium state after a short adjustment process under the action of a given input or external disturbance.
- Output position accuracy should be high. The accuracy of the servo system refers to the precise degree to which the output quantity can follow the input quantity. As a precision machining CNC machine tool, the required positioning accuracy or contouring accuracy is usually high, and the allowable deviation is generally between 0.01 and 0.00lmm. Static requirements for positioning accuracy and repeat positioning accuracy should be high, that is, positioning error and repeat positioning error should be small (to ensure dimensional accuracy). Dynamically, high following accuracy is required, i.e., the following error should be small, which is a dynamic performance indicator (to ensure the contour accuracy). In addition, high sensitivity and sufficiently high resolution are required.
- Fast response and no overshoot. Fast responsiveness is one of the signs of the dynamic quality of the servo system, that is, the response of the tracking command signal is required to be fast, on the one hand, the transition process time is required to be short, generally within 200ms, or even less than tens of milliseconds; on the other hand, in order to be satisfied with the overshooting requirements, it is required that the transition process of the leading edge of the steep, that is, the rate of rise should be large. This is the dynamic performance requirements of the servo system, that is, under the premise of no overshoot, the establishment time of the motion speed of the executive part should be as short as possible. Usually required from 0 → Fmax, its time should be less than 200ms, and there can be no overshooting, otherwise unfavorable to the mechanical components, harmful to the processing quality.
- The speed range should be wide and have good stability (within the speed range) speed range. Stability means that the fluctuation of the output speed should be less, especially in the low-speed smoothness is particularly important.
- Load characteristics should be hard in the system load range, when the load changes, the output speed should be basically unchanged. That is, △F is as small as possible. When the load changes suddenly, the recovery time of the speed is required to be short and without oscillation. That is, △t is as short as possible. In addition, there should be enough overload force. This is the requirement of CNC machine tool servo system has good static and dynamic stiffness.
Post a Comment:
You may also like:
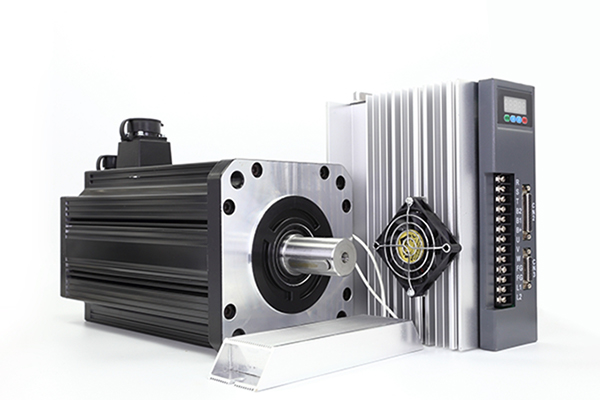
Category
Featured Articles
Servo Motor in Food Industry
In the ever-evolving landscape of the food industry, technological advancements play a pivotal role in enhancing efficiency, ...
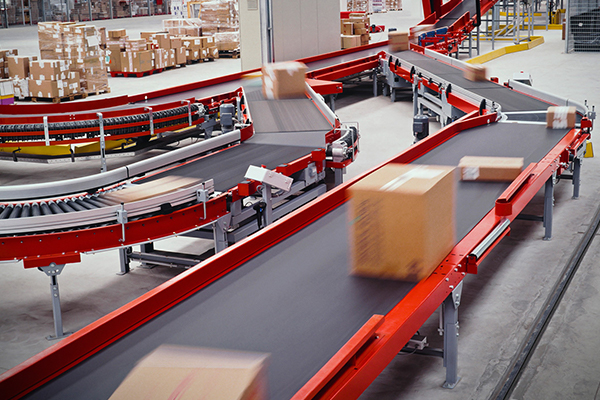
Servo Drives for Electric Mobility
Servo drives play a crucial role in electric mobility applications, providing precise control of electric motors for various ...
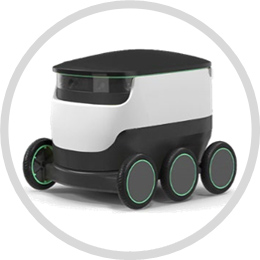
Servo Motor in Medical Industry
With the continuous development of technology, servo motors are being used more and more widely in medical equipment. Servo ...
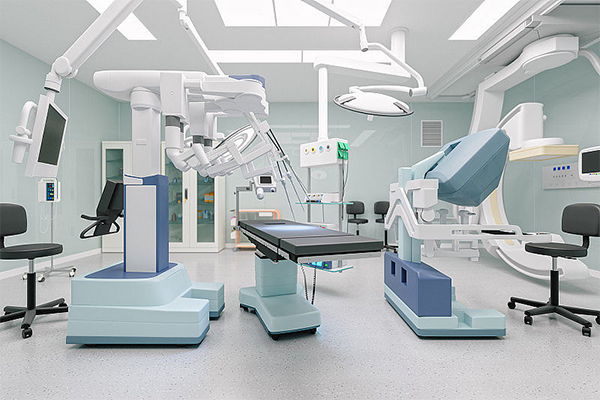
Equation Derivation for Servo Motor
In the analysis of electric servo drive motors , the equations for the motor indicates the presence of two time constants. One is ...
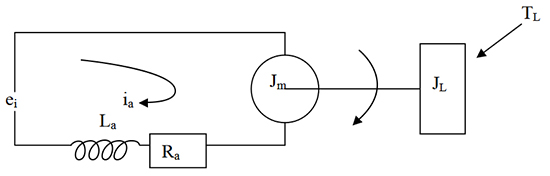
Servo System in CNC Machine Tools
As the actuator of CNC machine tools, servo system integrates power electronics, control, drive and protection, and with the ...
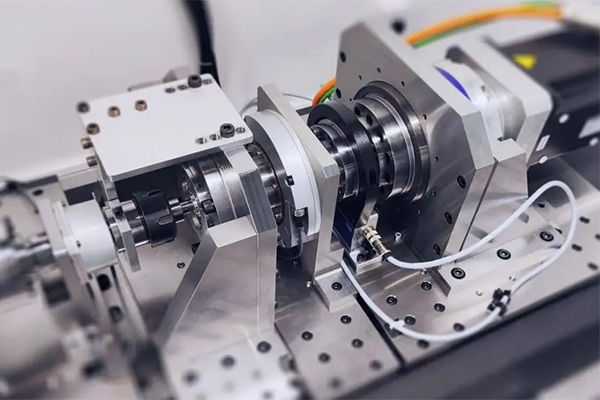