Home » Application » Servo Motors in Manufacturing
Servo Motors in Manufacturing
Introduction
Servo motors (or servos) are self-contained electric devices that rotate or push parts of a machine with great precision. Servos are found in many places: from toys to home electronics to cars and air-planes. If you have a radio-controlled model car, air-plane, or helicopter, you are using at least a few servos. In a model car or aircraft, servos move levers back and forth to control steering or adjust wing surfaces. By rotating a shaft connected to the engine throttle, a servo regulates the speed of a fuel-powered car or aircraft. Servos also appear behind the scenes in devices we use every day. Electronic devices such as DVD and Blueray DiscTM players use servos to extend or retract the disc trays. In 21st-century auto-mobiles, servos manage the car's speed: The gas pedal, similar to the volume control on a radio, sends an electrical signal that tells the car's computer how far down it is pressed. The car's computer calculates that information and other data from other sensors and sends a signal to the servo attached to the throttle to adjust the engine speed. Commercial aircraft use servos and a related hydraulic technology to push and pull just about everything in the plane.
The simplicity of a servo is among the features that make them so reliable. The heart of a servo is a small direct current (DC) motor, similar to what you might find in an inexpensive toy. These motors run on electricity from a battery and spin at high RPM (rotations per minute) but put out very low torque (a twisting force used to do work— you apply torque when you open a jar). An arrangement of gears takes the high speed of the motor and slows it down while at the same time increasing the torque. (Basic law of physics: work = force x distance.) A tiny electric motor does not have much torque, but it can spin really fast (small force, big distance). The gear design inside the servo case converts the output to a much slower rotation speed but with more torque (big force, little distance). The amount of actual work is the same, just more useful. Gears in an inexpensive servo motor are generally made of plastic to keep it lighter and less costly. On a servo designed to provide more torque for heavier work, the gears are made of metal and are harder to damage.
With a small DC motor, you apply power from a battery, and the motor spins. Unlike a simple DC motor, however, a servos spinning motor shaft is slowed way down with gears. A positional sensor on the final gear is connected to a small circuit board. The sensor tells this circuit board how far the servo output shaft has rotated. The electronic input signal from the computer or the radio in a remote-controlled vehicle also feeds into that circuit board. The electronics on the circuit board decode the signals to determine how far the user wants the servo to rotate. It then compares the desired position to the actual position and decides which direction to rotate the shaft so it gets to the desired position.

Product and its Application
Servos come in many sizes and in three basic types: positional rotation, continuous rotation, and linear. Positional rotation servo: this is the most common type of servo motor. The output shaft rotates in about half of a circle, or 180 degrees. It has physical stops placed in the gear mechanism to prevent turning beyond these limits to protect the rotational sensor. These common servos are found in radio-controlled cars and water- and aircraft, toys, robots, and many other applications.
Continuous rotation servo: this is quite similar to the common positional rotation servo motor, except it can turn in either direction indefinitely. The control signal, rather than setting the static position of the servo, is interpreted as the direction and speed of rotation. The range of possible commands causes the servo to rotate clockwise or counterclockwise as desired, at varying speed, depending on the command signal. You might use a servo of this type on a radar dish if you mounted one on a robot. Or you could use one as a drive motor on a mobile robot.
Linear servo: this is also like the positional rotation servo motor described above, but with additional gears (usually a rack and pinion mechanism) to change the output from circular to back-and-forth. These servos are not easy to find, but you can sometimes find them at hobby stores where they are used as actuators in larger model air-planes.
Industry Look out and Trends
Servo motors are high performance electric motors having characteristics such as controlling the movement of machines. In addition, servo motors offer easy installation and no maintenance cost. Increasing electricity prices and stringent electricity utilization standards are driving the demand for energy efficient motors globally. The market of servo drives and motors is expected to grow at a slower pace in North America and Europe region. The demand for servo drives and motors is expected to rise due to the replacement of outdated low efficient electric motors with highly efficient servo drives and motors. In addition, the strict energy consumption regulations and environment protection acts as the key factors that are driving the servo drives and motors market globally.
Servo motors (or servos) are self-contained electric devices that rotate or push parts of a machine with great precision. Servos are found in many places: from toys to home electronics to cars and air-planes. If you have a radio-controlled model car, air-plane, or helicopter, you are using at least a few servos. In a model car or aircraft, servos move levers back and forth to control steering or adjust wing surfaces. By rotating a shaft connected to the engine throttle, a servo regulates the speed of a fuel-powered car or aircraft. Servos also appear behind the scenes in devices we use every day. Electronic devices such as DVD and Blueray DiscTM players use servos to extend or retract the disc trays. In 21st-century auto-mobiles, servos manage the car's speed: The gas pedal, similar to the volume control on a radio, sends an electrical signal that tells the car's computer how far down it is pressed. The car's computer calculates that information and other data from other sensors and sends a signal to the servo attached to the throttle to adjust the engine speed. Commercial aircraft use servos and a related hydraulic technology to push and pull just about everything in the plane.
The simplicity of a servo is among the features that make them so reliable. The heart of a servo is a small direct current (DC) motor, similar to what you might find in an inexpensive toy. These motors run on electricity from a battery and spin at high RPM (rotations per minute) but put out very low torque (a twisting force used to do work— you apply torque when you open a jar). An arrangement of gears takes the high speed of the motor and slows it down while at the same time increasing the torque. (Basic law of physics: work = force x distance.) A tiny electric motor does not have much torque, but it can spin really fast (small force, big distance). The gear design inside the servo case converts the output to a much slower rotation speed but with more torque (big force, little distance). The amount of actual work is the same, just more useful. Gears in an inexpensive servo motor are generally made of plastic to keep it lighter and less costly. On a servo designed to provide more torque for heavier work, the gears are made of metal and are harder to damage.
With a small DC motor, you apply power from a battery, and the motor spins. Unlike a simple DC motor, however, a servos spinning motor shaft is slowed way down with gears. A positional sensor on the final gear is connected to a small circuit board. The sensor tells this circuit board how far the servo output shaft has rotated. The electronic input signal from the computer or the radio in a remote-controlled vehicle also feeds into that circuit board. The electronics on the circuit board decode the signals to determine how far the user wants the servo to rotate. It then compares the desired position to the actual position and decides which direction to rotate the shaft so it gets to the desired position.

Servos come in many sizes and in three basic types: positional rotation, continuous rotation, and linear. Positional rotation servo: this is the most common type of servo motor. The output shaft rotates in about half of a circle, or 180 degrees. It has physical stops placed in the gear mechanism to prevent turning beyond these limits to protect the rotational sensor. These common servos are found in radio-controlled cars and water- and aircraft, toys, robots, and many other applications.
Continuous rotation servo: this is quite similar to the common positional rotation servo motor, except it can turn in either direction indefinitely. The control signal, rather than setting the static position of the servo, is interpreted as the direction and speed of rotation. The range of possible commands causes the servo to rotate clockwise or counterclockwise as desired, at varying speed, depending on the command signal. You might use a servo of this type on a radar dish if you mounted one on a robot. Or you could use one as a drive motor on a mobile robot.
Linear servo: this is also like the positional rotation servo motor described above, but with additional gears (usually a rack and pinion mechanism) to change the output from circular to back-and-forth. These servos are not easy to find, but you can sometimes find them at hobby stores where they are used as actuators in larger model air-planes.
Industry Look out and Trends
Servo motors are high performance electric motors having characteristics such as controlling the movement of machines. In addition, servo motors offer easy installation and no maintenance cost. Increasing electricity prices and stringent electricity utilization standards are driving the demand for energy efficient motors globally. The market of servo drives and motors is expected to grow at a slower pace in North America and Europe region. The demand for servo drives and motors is expected to rise due to the replacement of outdated low efficient electric motors with highly efficient servo drives and motors. In addition, the strict energy consumption regulations and environment protection acts as the key factors that are driving the servo drives and motors market globally.
Post a Comment:
You may also like:
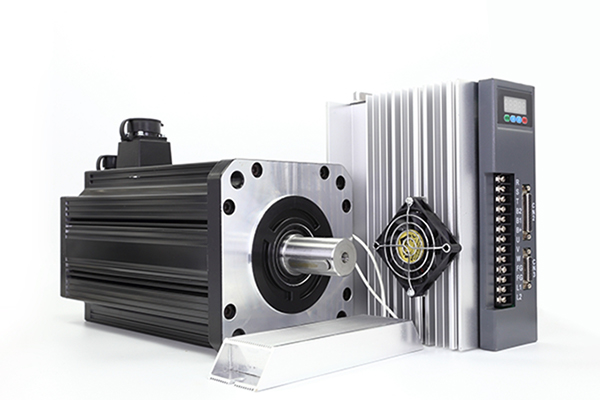
Category
Featured Articles
Servo Motor in Medical Industry
With the continuous development of technology, servo motors are being used more and more widely in medical equipment. Servo ...
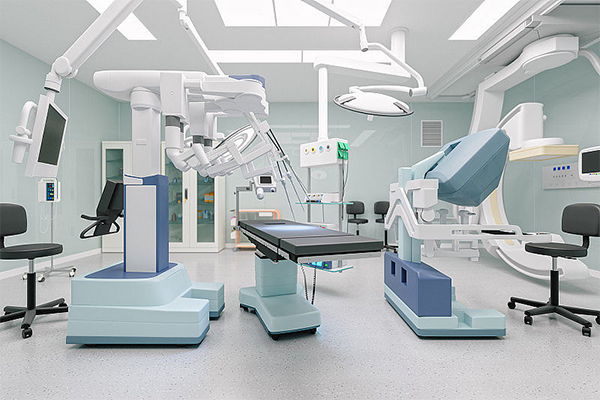
Servo System in CNC Machine Tools
As the actuator of CNC machine tools, servo system integrates power electronics, control, drive and protection, and with the ...
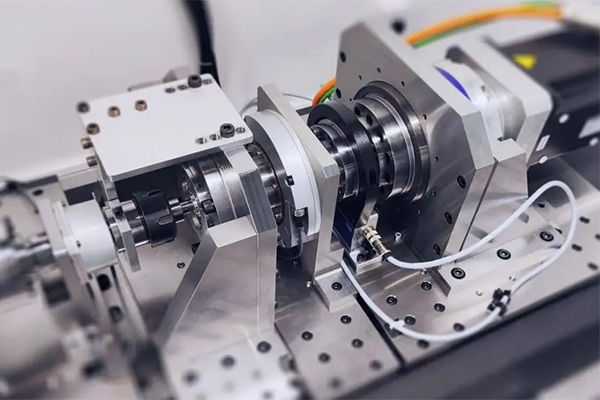
Equation Derivation for Servo Motor
In the analysis of electric servo drive motors , the equations for the motor indicates the presence of two time constants. One is ...
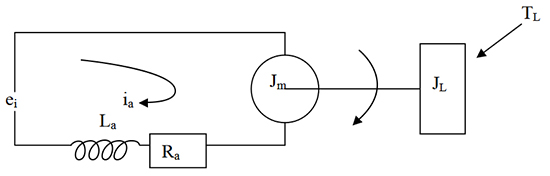
Servo Drives for Electric Mobility
Servo drives play a crucial role in electric mobility applications, providing precise control of electric motors for various ...
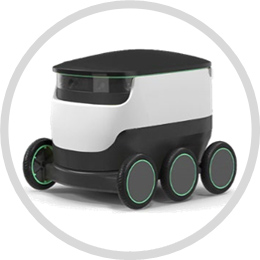
Servo Motor in Food Industry
In the ever-evolving landscape of the food industry, technological advancements play a pivotal role in enhancing efficiency, ...
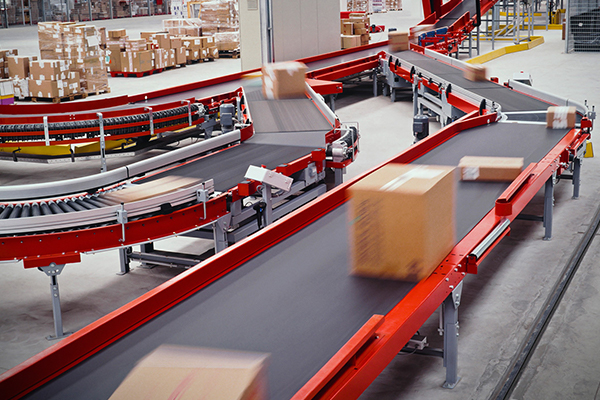