Home » Servo Drive » Servo Drive System vs. Variable Frequency Drive
Servo Drive System vs. Variable Frequency Drive
Variable Frequency Drive
A variable frequency drive (VFD) is also a motor control unit, but it works in a different way than a servo drive. The VFD is a type of motor controller that works in conjunction with an electric motor by varying the variables such as voltage and frequency supplied to the electric motor. While a servo drive needs a command signal given to the motor in order to compare the real and desired position of the motor, a VFD directly controls the voltage and frequency supplied to the motor. VFDs are also known by other names such as AC drive, adjustable-frequency drive, inverter.
When it comes to the motor's speed (RPM), a variable that is directly related is the frequency in Hz. The lower the frequency is, the lower the speed of the motor is, and vice versa. Sometimes, the electric motor doesn't need to run at full speed and VFD can come in handy since it allows you to manipulate the frequency and voltage. If you don't need full speed, you can decrease the frequency and voltage of the motor to suit your needs. This will also save the electric motor from potential malfunction and extend its life.
Generally, variable frequency drives are used for reducing energy consumption thus reducing the energy costs of an electric motor. These motor proved to be very good when it comes to tight process control and are used everywhere from small appliances to large electronic systems, for controlling electric motors.
Servo Drive
A servo drive is an integral part of a servo system that consists of a motor, a controller, a feedback device, and of course a servo drive. In a laymans language a servo drive is a part of the servo system that receives a particular command from a control system, amplifies it, and transmits the current to a servo motor in the system. The servo motor produces a motion,tailored to the command it has received. The command signal usually represents some of the physical variables such as torque, velocity, and the desired position.
The servo motor is equipped with a sensor (Encoder) that reads the current position of the motor and reports it back to the servo drive. when the feedback is received, a servo drive compares the motor status and position with the commanded variables. If there's a deviation from the given commands, the servo drive alters the frequency, voltage or any other variable to correct the deviations.
Servo Drive System vs.Variable Frequency Drive
A servo drive system, as opposed to a variable frequency drive (VFD) or AC motor drive , has the ability to position with extreme precision and repeatability. While a VFD can be configured for position control, it cannot attain the exactness of a servo drive. VFDs are also available in much higher horsepower ranges than servo's. Selection of external feedback sensors such as encoders, resolvers, linear position sensors, etc., required to achieve closed-loop control and each having its own inherent precision, will enable the system accuracy accordingly. Your application requirements will always dictate which system configuration will give you the best results. Many of today's VFDs are fully capable of doing positioning when using encoder feedback; as with many other things, the lines have become blurred. What separates servo motor from induction motors is their low inertia and their ability to accelerate and decelerate much faster, the trick is to decide when you need full servo performance.
Using variable frequency drive (VFD) for the servo application is quite possible, provided the application is less demanding in critical positioning purpose. Servo motors have different information on motor control it includes rotor positioning feedback, VECTOR mode, requires motor recognition and not necessary and encoder for rotor feedback, it estimates it through output current. Numerical Commands can set V/F set point on power modules usually. When you have vector and Torque control, you may have a torque set point, instead of speed set point, if there's no load on this mode, the motor speeds up fast and may damage mechanics. If you control Torque, with the same power, speed becomes uncontrollable, some applications combine torque and speed set points for different frequency / torque ranges. The problem here is that we are trying to define a specific answer using very general terms. A servo motor can be an induction servo, a brushless servo, a reluctance servo a dc servo- each of these can be either linear or rotary and can come with a variety of feedback such as tachometer, resolver of various pole counts, incremental or absolute encoders discreet or serial interface with different bus options, laser feedback, halls etc.
Then you come to the term variable frequency drive. Brushless servo amplifiers are also vfds. Do standard inverters have proper control of induction, and brushless motors. Some allow for a software switch, some allow for a firmware download, some don't.will inverters accept feedback some have it built in, most that allow it do so by option cards, many do not.
A variable frequency drive (VFD) is also a motor control unit, but it works in a different way than a servo drive. The VFD is a type of motor controller that works in conjunction with an electric motor by varying the variables such as voltage and frequency supplied to the electric motor. While a servo drive needs a command signal given to the motor in order to compare the real and desired position of the motor, a VFD directly controls the voltage and frequency supplied to the motor. VFDs are also known by other names such as AC drive, adjustable-frequency drive, inverter.
When it comes to the motor's speed (RPM), a variable that is directly related is the frequency in Hz. The lower the frequency is, the lower the speed of the motor is, and vice versa. Sometimes, the electric motor doesn't need to run at full speed and VFD can come in handy since it allows you to manipulate the frequency and voltage. If you don't need full speed, you can decrease the frequency and voltage of the motor to suit your needs. This will also save the electric motor from potential malfunction and extend its life.
Generally, variable frequency drives are used for reducing energy consumption thus reducing the energy costs of an electric motor. These motor proved to be very good when it comes to tight process control and are used everywhere from small appliances to large electronic systems, for controlling electric motors.

A servo drive is an integral part of a servo system that consists of a motor, a controller, a feedback device, and of course a servo drive. In a laymans language a servo drive is a part of the servo system that receives a particular command from a control system, amplifies it, and transmits the current to a servo motor in the system. The servo motor produces a motion,tailored to the command it has received. The command signal usually represents some of the physical variables such as torque, velocity, and the desired position.
The servo motor is equipped with a sensor (Encoder) that reads the current position of the motor and reports it back to the servo drive. when the feedback is received, a servo drive compares the motor status and position with the commanded variables. If there's a deviation from the given commands, the servo drive alters the frequency, voltage or any other variable to correct the deviations.
Servo Drive System vs.Variable Frequency Drive
A servo drive system, as opposed to a variable frequency drive (VFD) or AC motor drive , has the ability to position with extreme precision and repeatability. While a VFD can be configured for position control, it cannot attain the exactness of a servo drive. VFDs are also available in much higher horsepower ranges than servo's. Selection of external feedback sensors such as encoders, resolvers, linear position sensors, etc., required to achieve closed-loop control and each having its own inherent precision, will enable the system accuracy accordingly. Your application requirements will always dictate which system configuration will give you the best results. Many of today's VFDs are fully capable of doing positioning when using encoder feedback; as with many other things, the lines have become blurred. What separates servo motor from induction motors is their low inertia and their ability to accelerate and decelerate much faster, the trick is to decide when you need full servo performance.

Then you come to the term variable frequency drive. Brushless servo amplifiers are also vfds. Do standard inverters have proper control of induction, and brushless motors. Some allow for a software switch, some allow for a firmware download, some don't.will inverters accept feedback some have it built in, most that allow it do so by option cards, many do not.
Post a Comment:
You may also like:
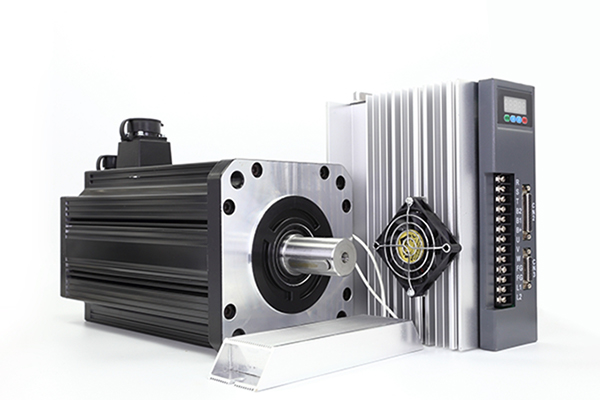
Category
Featured Articles
What are the Basics of Servo Drive?
Servo motors come in so many types and flavors that it is difficult to define them in a way that is accurate and universally ...
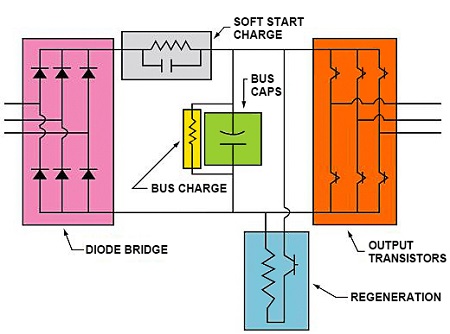
How to Install a Servo Drive?
Installing a servo drive involves several steps, and the specific process may vary depending on the manufacturer and model of the ...

What are the Soft Start Techniques for ...
Servos (as commonly used in radio-controlled vehicles and small-scale robotics)are DC actuators that use a potentiometer to ...

Servo Drive System vs. Variable ...
A servo drive system, as opposed to a variable frequency drive (VFD) or AC motor drive , has the ability to position with ...
