Servo Compensation Method for Servo System
A simple damper consists of an inertia slug coupled viscous to the motor shaft. The heavy inertia slug is mounted on ball bearings riding on the motor shaft and is surrounded by a light fluid-tight shell pinned directly to the motor shaft. The space between the shell and the inertia slug is filled with a silicone-damping fluid. A practical way of looking at the damper is that, for small high-frequency oscillations, the damper acts like a direct viscous drag to stabilize the electric servo. At sustained motor velocities, however, the slug eventually attains the same speed as the servo motor. This property overcomes the major disadvantage of direct viscous friction damping because no power is dissipated at constant velocities.
Because the damper is a load compensation device, rather than a cascade or feed-back device, the amplifier need provide only AC gain from the synchro to the AC control motor. This feature minimizes any possibility of drift, which was one of the design goals.

For equal servo bandwidths, however, the
damper-compensated servo has considerable advantage over both lead-network
compensation and tachometer compensation. A lead network provides a high
velocity constant and a relatively low torque constant, whereas tachometer feedback
provides a high torque constant and a relatively low velocity constant. A
damper provides both a high torque constant and a very high velocity constant.
Because of the large increase in
motor-shaft inertia, the damper provides a transfer function that can only be
duplicated by either a combination of tachometer feedback and an integral
network or a tachometer feedback with a high-pass filter, both of which would
require DC networks. A high torque constant at zero frequency is desirable to
combat friction errors. The damper has an additional advantage in that it
directly attenuates any system noise that may have reached the motor shaft.
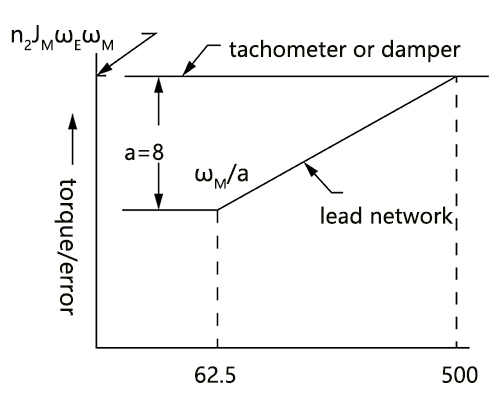
The damper-compensated servo is insensitive to power-supply voltage changes, since a ±2:1 change in loop gain is possible with negligible change in performance. Also, because there are no frequency-sensitive elements such as load networks, the servo is insensitive to changes in the prime power frequency which excites the synchros and the industrial servo motor.
The servo operates without noticeable change for power frequencies of 400±100 cps. The high torque constant makes the repeater insensitive to vibration. The only remaining problem, therefore, is the effect of temperature on the viscous damping fluid. Silicone fluid has excellent temperature characteristics, and a variation of ±50°F results in negligible performance change in the servo. For airborne applications, a heater and thermostat are generally used to keep the damper at 160 ± 259F.
Post a Comment:
You may also like:
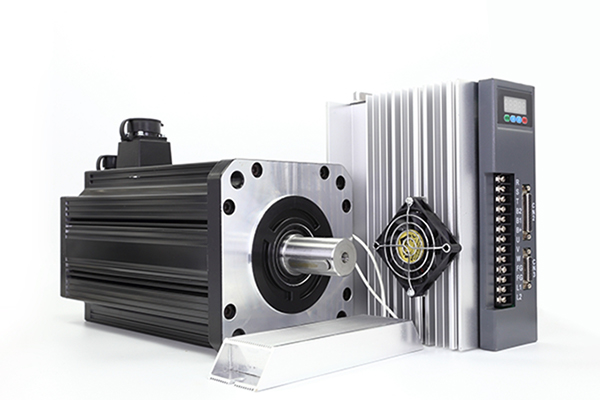


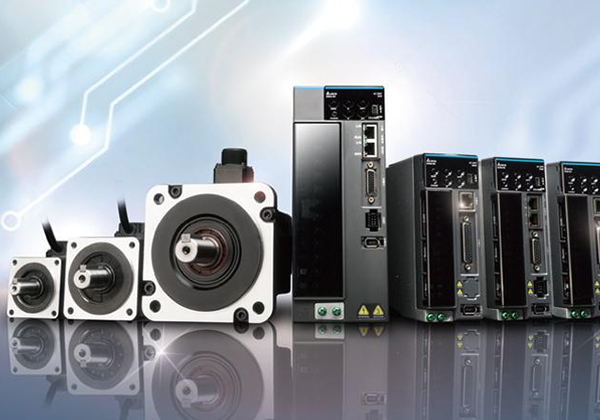
