Home » Servo System » Hydraulic Servo Systems--Theory and Applications
Hydraulic Servo Systems--Theory and Applications
When closed-loop hydraulic control systems first began to appear in industry, the applications were generally those in which very high performance was required. While hydraulic servo systems are still heavily used in high-performance applications such as the machine-tool industry, they are beginning to gain wide acceptance in a variety of industries. Examples are material handling, mobile equipment, plastics, steel plants, mining, oil exploration, and automotive testing. Closed loop servo drive technology is increasingly becoming the norm in machine automation, where the operators are demanding greater precision, faster operation, and simpler adjustment. There is also an expectation that the price of increasing the level of automation should be contained within acceptable limits.
What is a servo?
In its simplest form, a servo or a servomechanism is a servo control system that measures its output and forces the output to quickly and accurately follow a command signal. In this way, the effect of anomalies in the control device itself and the load can be minimized as well as the influence of external disturbances. A servomechanism can be designed to control almost any physical quantity, e.g. motion, force, pressure, temperature, electrical voltage, or current.
Technology comparisons
The potential for alternative technologies should be assessed in light of the well-known capabilities of electro-pneumatic and electro-mechanical servos. A high-performance actuation system is characterized by wide bandwidth frequency response, low resolution, and high stiffness. Additional requirements may include demanding duty cycles and minimization of size and weight. The last-mentioned requirements are of special interest in aerospace applications. The most important selection criteria can be summarized as follows:
The above figure indicates that applications in the lower range of power and dynamic response may also be satisfied with electro-pneumatic servos. However, the best choice is always determined by considerations, such as the selection criteria discussed above. In most applications, the aspect of cost is generally dominant.
Experience indicates that electro-mechanical or electro-pneumatic actuators tend to have lower costs than electro-hydraulic actuators in the low-performance range. This cost difference rapidly dissipates for applications that require high power and/or high dynamic response.
In comparing costs, one must be careful to consider the total cost of the entire servo-actuation system. The higher cost of an electro-hydraulic servo often results from the power conversion equipment needed to provide high-pressure fluid with a low contamination level. It is also clear that the relative cost of an alternative actuation system designed for a specific application will depend, primarily, on the actuation power level.
Capabilities of electro-hydraulic servos
When rapid and precise control of sizeable loads is required an electro-hydraulic servo is often the best approach to the problem. Generally speaking, the hydraulic servo actuator provides fast response, high force, and short stroke characteristics. The main advantages of hydraulic components are.
What is a servo?
In its simplest form, a servo or a servomechanism is a servo control system that measures its output and forces the output to quickly and accurately follow a command signal. In this way, the effect of anomalies in the control device itself and the load can be minimized as well as the influence of external disturbances. A servomechanism can be designed to control almost any physical quantity, e.g. motion, force, pressure, temperature, electrical voltage, or current.

Technology comparisons
The potential for alternative technologies should be assessed in light of the well-known capabilities of electro-pneumatic and electro-mechanical servos. A high-performance actuation system is characterized by wide bandwidth frequency response, low resolution, and high stiffness. Additional requirements may include demanding duty cycles and minimization of size and weight. The last-mentioned requirements are of special interest in aerospace applications. The most important selection criteria can be summarized as follows:
- Cost
- Size and weight
- Duty cycle
- Environment: Vibration, shock, temperature, etc.
The above figure indicates that applications in the lower range of power and dynamic response may also be satisfied with electro-pneumatic servos. However, the best choice is always determined by considerations, such as the selection criteria discussed above. In most applications, the aspect of cost is generally dominant.
Experience indicates that electro-mechanical or electro-pneumatic actuators tend to have lower costs than electro-hydraulic actuators in the low-performance range. This cost difference rapidly dissipates for applications that require high power and/or high dynamic response.
In comparing costs, one must be careful to consider the total cost of the entire servo-actuation system. The higher cost of an electro-hydraulic servo often results from the power conversion equipment needed to provide high-pressure fluid with a low contamination level. It is also clear that the relative cost of an alternative actuation system designed for a specific application will depend, primarily, on the actuation power level.
Capabilities of electro-hydraulic servos
When rapid and precise control of sizeable loads is required an electro-hydraulic servo is often the best approach to the problem. Generally speaking, the hydraulic servo actuator provides fast response, high force, and short stroke characteristics. The main advantages of hydraulic components are.
- Easy and accurate control of work table position and velocity
- Good stiffness characteristics
- Zero backlash
- Rapid response to changes in speed or direction
- Low rate of wear
- Hydraulic drives have substantially higher power-to-weight ratios resulting in higher machine frame resonant frequencies for a given power level.
- Hydraulic actuators are stiffer than electric drives, resulting in higher loop gain capability, greater accuracy, and better frequency response.
- Hydraulic servos give smoother performance at low speeds and have a wide speed range without special control circuits.
- Hydraulic systems are to a great extent self-cooling and can be operated in stall condition indefinitely without damage.
- Both hydraulic and electric drives are very reliable provided that maintenance is followed.
- Hydraulic servos are usually less expensive for systems above several horsepower, especially if the hydraulic power supply is shared between several actuators.
Post a Comment:
You may also like:
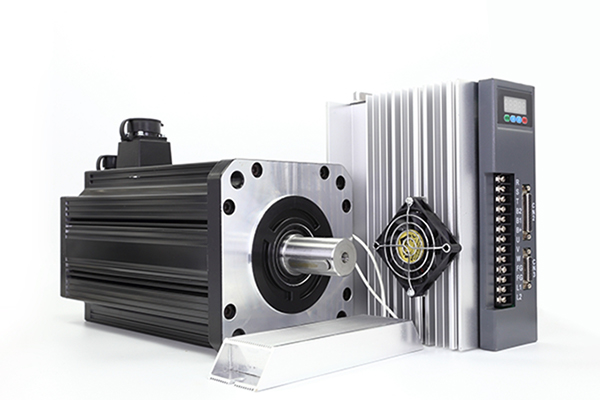
Category
Featured Articles
What are the Basic Components of ...
Servomechanisms, called servos for short, are the basic building blocks of power drives. In this manual what we mean by a power ...

What is the Bandwidth of ...
For a servo system, the bandwidth is the maximum sine wave frequency to which the servo system can respond. In professional ...

What Should Consider Before Using ...
Servo system is a commonly used control system, widely used in industrial automation. It compares the output signal with the ...
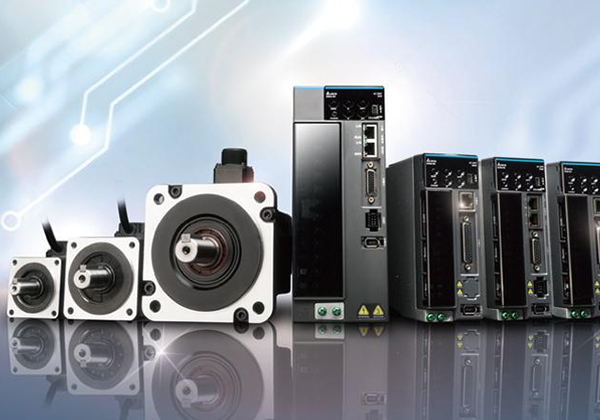
What is Servo System?
A feedback control system used to precisely follow or reproduce a process. Also known as a follower system. In many cases, a ...
