Home » Servo System » How to Realize Servo Control S-Curve Acceleration and Aeceleration PLC?
How to Realize Servo Control S-Curve Acceleration and Aeceleration PLC?
In the field of industrial automation, servo control is an important motion control method. S-curve acceleration and deceleration is a commonly used motion control curve in servo system. In this paper, we will discuss the principle of S-curve acceleration and deceleration in servo control and the method of PLC implementation, in order to help readers better understand and apply this technology.
Servo Control Overview
Servo control is a high-precision, high-sensitivity motion control method, usually used in applications that require precise control of position, speed and force. Compared with traditional stepping control, servo control has the advantages of fast response speed and good stability, so it is widely used in industrial machinery, medical equipment, aerospace and other fields. In servo control, S-curve acceleration and deceleration is a control curve. It is characterised by slow speed changes in the start and termination phases, and fast acceleration and deceleration in the middle phase, which can effectively reduce the impact and vibration in the motion process and improve the stability and accuracy of the system.
The Importance of S-curve Acceleration and Deceleration in Servo Control
S-curve acceleration and deceleration is of great significance in servo control. Servo control, as a high-precision and high-stability motion control method, plays a crucial role in the application of industrial automation. In practice, servo control systems often need to complete complex motion tasks, including position, speed and force control. The S-curve acceleration and deceleration can effectively reduce the impact and vibration of the system movement process, improve the stability and accuracy of the system, thus ensuring the quality and effectiveness of the system's motion control. In the field of industrial machinery, especially on the production line with high precision requirements, the servo control system often needs to complete some complex motion tasks, such as processing, assembly and testing. And in these motion processes, speed and acceleration and deceleration control is particularly important. The traditional acceleration and deceleration programme is likely to lead to system shock and vibration at the beginning and end stages, reducing the stability and accuracy of the system. S-curve acceleration and deceleration is designed to solve this problem, which provides a smooth acceleration and deceleration process, effectively reduces the shock and vibration of the system, and ensures the smoothness and accuracy of the system motion process.
S-curve Acceleration and Deceleration Method
In practical applications, the use of PLC to achieve S-curve acceleration and deceleration is a common method, PLC as a computer dedicated to industrial control, with high-speed, stable characteristics, can achieve complex control algorithms. In practical applications, S-curve acceleration and deceleration algorithm can be achieved through programming, including speed and position control.
Specifically, the high-speed computing power of the PLC can be used to achieve S-curve acceleration and deceleration algorithms through programming. In PLC programming, mathematical models can be used to describe the laws of S-curve acceleration and deceleration, and then control the output signal to achieve the speed control of the servo system. It can also be combined with the position and speed information fed back by the sensor to achieve closed-loop control, which further improves the stability and accuracy of the system.
In practical applications, according to the specific needs and the actual situation, combined with the experience and technology of engineers, to further optimise and improve the S-curve acceleration and deceleration algorithms, in order to achieve more efficient and stable motion control. S-curve parameters, such as start speed, end speed, acceleration and deceleration, can be adjusted to achieve better control of the system's motion characteristics. By optimising the S-curve acceleration and deceleration algorithm, the smoothness and accuracy of the system can be further improved to meet the needs of various complex motion control tasks.
Case Study in Practical Applications
In order to further illustrate the importance and effect of S-curve acceleration and deceleration in practical applications, an actual case can be analysed.
Take an assembly line as an example, there is a workpiece that needs to be assembled precisely, and it needs to complete the precise control of position, speed and force during the assembly process. Under the traditional acceleration and deceleration control scheme, the system is prone to shock and vibration, thus affecting the assembly accuracy of the workpiece. The S-curve acceleration and deceleration control scheme can effectively reduce the shock and vibration of the system at the beginning and end stages, ensuring the smoothness and accuracy of the workpiece assembly process.
In practice, the motion control effect of the assembly line can be further improved by optimising the S-curve acceleration and deceleration algorithm. According to the characteristics of the assembled workpiece and process requirements, the parameters of the S-curve can be adjusted, such as start speed, end speed, acceleration and deceleration, to achieve better control of the workpiece assembly process. By optimising the S-curve acceleration and deceleration algorithm, it can not only improve the smoothness of motion and assembly accuracy of the assembly line, but also reduce the noise and vibration generated by the system in the process of motion, prolonging the service life of the system and reducing the maintenance cost.
The application of S-curve acceleration and deceleration in servo control can not only improve the motion smoothness and control accuracy of the system, but also reduce the vibration and shock of the system in the process of motion, thus extending the service life of the system. In practice, the use of PLC makes the implementation of S-curve acceleration and deceleration become more flexible and convenient, but also provides engineers with more control means and algorithm optimisation possibilities.
Summary
S-curve acceleration and deceleration is of great significance in servo control, which can effectively improve the smoothness of the system movement and control accuracy, reduce the impact and vibration of the system in the process of movement, and ensure the quality and effect of the system's motion control. In practice, the use of PLC to achieve S-curve acceleration and deceleration is a common method, through the optimisation of the S-curve acceleration and deceleration algorithm, you can further improve the motion control effect of the system, which is widely used in the field of industrial automation.
Servo Control Overview
Servo control is a high-precision, high-sensitivity motion control method, usually used in applications that require precise control of position, speed and force. Compared with traditional stepping control, servo control has the advantages of fast response speed and good stability, so it is widely used in industrial machinery, medical equipment, aerospace and other fields. In servo control, S-curve acceleration and deceleration is a control curve. It is characterised by slow speed changes in the start and termination phases, and fast acceleration and deceleration in the middle phase, which can effectively reduce the impact and vibration in the motion process and improve the stability and accuracy of the system.
The Importance of S-curve Acceleration and Deceleration in Servo Control
S-curve acceleration and deceleration is of great significance in servo control. Servo control, as a high-precision and high-stability motion control method, plays a crucial role in the application of industrial automation. In practice, servo control systems often need to complete complex motion tasks, including position, speed and force control. The S-curve acceleration and deceleration can effectively reduce the impact and vibration of the system movement process, improve the stability and accuracy of the system, thus ensuring the quality and effectiveness of the system's motion control. In the field of industrial machinery, especially on the production line with high precision requirements, the servo control system often needs to complete some complex motion tasks, such as processing, assembly and testing. And in these motion processes, speed and acceleration and deceleration control is particularly important. The traditional acceleration and deceleration programme is likely to lead to system shock and vibration at the beginning and end stages, reducing the stability and accuracy of the system. S-curve acceleration and deceleration is designed to solve this problem, which provides a smooth acceleration and deceleration process, effectively reduces the shock and vibration of the system, and ensures the smoothness and accuracy of the system motion process.

In practical applications, the use of PLC to achieve S-curve acceleration and deceleration is a common method, PLC as a computer dedicated to industrial control, with high-speed, stable characteristics, can achieve complex control algorithms. In practical applications, S-curve acceleration and deceleration algorithm can be achieved through programming, including speed and position control.
Specifically, the high-speed computing power of the PLC can be used to achieve S-curve acceleration and deceleration algorithms through programming. In PLC programming, mathematical models can be used to describe the laws of S-curve acceleration and deceleration, and then control the output signal to achieve the speed control of the servo system. It can also be combined with the position and speed information fed back by the sensor to achieve closed-loop control, which further improves the stability and accuracy of the system.
In practical applications, according to the specific needs and the actual situation, combined with the experience and technology of engineers, to further optimise and improve the S-curve acceleration and deceleration algorithms, in order to achieve more efficient and stable motion control. S-curve parameters, such as start speed, end speed, acceleration and deceleration, can be adjusted to achieve better control of the system's motion characteristics. By optimising the S-curve acceleration and deceleration algorithm, the smoothness and accuracy of the system can be further improved to meet the needs of various complex motion control tasks.
Case Study in Practical Applications
In order to further illustrate the importance and effect of S-curve acceleration and deceleration in practical applications, an actual case can be analysed.
Take an assembly line as an example, there is a workpiece that needs to be assembled precisely, and it needs to complete the precise control of position, speed and force during the assembly process. Under the traditional acceleration and deceleration control scheme, the system is prone to shock and vibration, thus affecting the assembly accuracy of the workpiece. The S-curve acceleration and deceleration control scheme can effectively reduce the shock and vibration of the system at the beginning and end stages, ensuring the smoothness and accuracy of the workpiece assembly process.
In practice, the motion control effect of the assembly line can be further improved by optimising the S-curve acceleration and deceleration algorithm. According to the characteristics of the assembled workpiece and process requirements, the parameters of the S-curve can be adjusted, such as start speed, end speed, acceleration and deceleration, to achieve better control of the workpiece assembly process. By optimising the S-curve acceleration and deceleration algorithm, it can not only improve the smoothness of motion and assembly accuracy of the assembly line, but also reduce the noise and vibration generated by the system in the process of motion, prolonging the service life of the system and reducing the maintenance cost.
The application of S-curve acceleration and deceleration in servo control can not only improve the motion smoothness and control accuracy of the system, but also reduce the vibration and shock of the system in the process of motion, thus extending the service life of the system. In practice, the use of PLC makes the implementation of S-curve acceleration and deceleration become more flexible and convenient, but also provides engineers with more control means and algorithm optimisation possibilities.
Summary
S-curve acceleration and deceleration is of great significance in servo control, which can effectively improve the smoothness of the system movement and control accuracy, reduce the impact and vibration of the system in the process of movement, and ensure the quality and effect of the system's motion control. In practice, the use of PLC to achieve S-curve acceleration and deceleration is a common method, through the optimisation of the S-curve acceleration and deceleration algorithm, you can further improve the motion control effect of the system, which is widely used in the field of industrial automation.
Post a Comment:
You may also like:
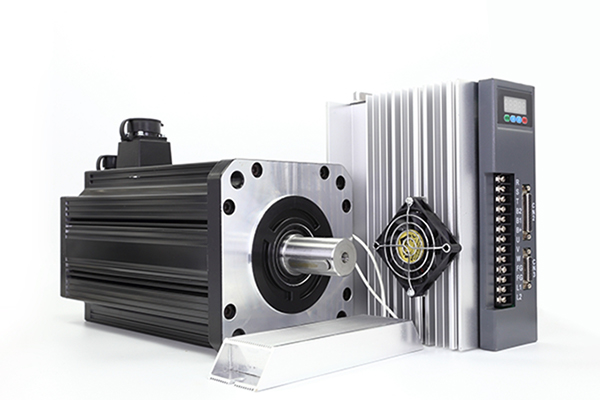
Category
Featured Articles
What are the Basic Components of ...
Servomechanisms, called servos for short, are the basic building blocks of power drives. In this manual what we mean by a power ...

What is Servo System?
A feedback control system used to precisely follow or reproduce a process. Also known as a follower system. In many cases, a ...

What is the Bandwidth of ...
For a servo system, the bandwidth is the maximum sine wave frequency to which the servo system can respond. In professional ...

What Should Consider Before Using ...
Servo system is a commonly used control system, widely used in industrial automation. It compares the output signal with the ...
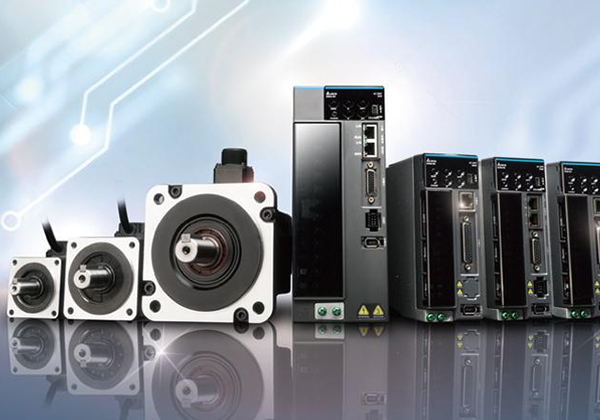