Home » Application » How to Improve Wind Power Generation by using Servo Motor?
How to Improve Wind Power Generation by using Servo Motor?
A servomotor is a rotary actuator that allows for precise control of angular position, velocity, and acceleration. It consists of a suitable motor coupled to a sensor for position feedback. It also requires a relatively sophisticated controller, often a dedicated module designed specifically for use with servomotors. Servomotors are not a specific class of motor although the term servomotor is often used to refer to a motor suitable for use in a closed-loop control system. Servomotors are used in applications such as robotics, CNC machinery, or automated manufacturing. This paper presented an excitation synchronous wind power generator with MPTC scheme. In the proposed framework, the servo motor provides controllable power to regulate the rotor speed and voltage phase under wind disturbance. Using a phase tracking control strategy, the proposed system can achieve smaller voltage phase deviations in the excitation synchronous generator. In addition, the maximum output power tracking scheme governs the input and output powers to achieve high performance.
Servo Motor Controller Design
The transient and dynamic responses of the servo motor controller must satisfy robustness requirements to reduce the influence of wind fluctuations on the generator. Thus, the robust integral structure control (RISC) method is chosen to ensure the voltage phase and the frequency in phase with the grid. Among general electrical motors, the three-phase PM synchronous motor has the advantages of high-efficiency and low-maintenance requirements, the reason controllable power for the servo control structure was chosen in the research. Wind power, generator power, and servo motor power can be transformed into three torque functions and incorporated into the three-phase PM synchronous motor model. The electromagnetic torque of the servo motor can be expressed as:
The RISC outer loop is designed to achieve a fast and accurate servo tracking response under load disturbances and plant parameter variations.The position command. Parameters and are proportional gains and is the integral gain. The PM synchronous motor state equations are described as:
Before the excitation synchronous generator system connects to the grid, equals the grid voltage angle. With the coaxial configuration described, the servo motor and generator electrical angle can be obtained using the motor encoder and the grid voltage sensor, respectively. The MCU compares the phase difference between the two signals and gradually adjusts the excitation synchronous generator rotor position to reduce the phase deviation.
Maximum Power Tracking Control
In a natural environment, wind power varies with time. To stabilize the generator output voltage, current, and output power, the excitation synchronous generator output power has to track the input power variation and react immediately by adjusting the excitation field current. In this paper, a maximum power tracking control scheme is proposed. The proposed MPTC scheme includes two control loops, which are the motor power control loop, and the generator power control loop. By MPTC scheme, can make the motor consumption power and most of the wind power can be transferred to the grid by the generator.
If an air dynamic occurs in the wind turbine, the servo motor responds to this change to maintain the generator speed constant. The three-phase servo motor power is calculated and compared to the servo motor command. In this state, the servo motor command is set equal to zero. The servo motor deviation signal command passes by the motor power control loop to obtain the signal. As is expected, in the steady state, the servo motor consumes less power.
In the generator power control loop, the three-phase voltages , and currents of the excitation synchronous generator power output are fed back for comparison with the generator power command. This power deviation passes the PI controller and the excitation gain generates a corresponding excitation field current control signal. Thus the excitation synchronous generator output power can track the generator power command.
Servo Motor Controller Design
The transient and dynamic responses of the servo motor controller must satisfy robustness requirements to reduce the influence of wind fluctuations on the generator. Thus, the robust integral structure control (RISC) method is chosen to ensure the voltage phase and the frequency in phase with the grid. Among general electrical motors, the three-phase PM synchronous motor has the advantages of high-efficiency and low-maintenance requirements, the reason controllable power for the servo control structure was chosen in the research. Wind power, generator power, and servo motor power can be transformed into three torque functions and incorporated into the three-phase PM synchronous motor model. The electromagnetic torque of the servo motor can be expressed as:
Tm=P/2λm*[IU*sinθr+IV*sin(θr-2/3π)+IW*sin(θr-4/3π)]
where denotes the number of motor poles, and are the applied stator currents. The mechanical torque can be expressed as:
Tm+(Tw-Tg)=Js(2/P)dωr/dt+B(2/P)ωr
θr=∫ωrdt
θm=2/Pθr
Additionally, denotes the electrical rotor angular velocity; represents the electrical rotor angular displacement; is the mechanical rotor angular displacement; is the rotor inertia; and is the damping coefficient. Moreover, is the electrical time constant, and is the mechanical time constant. It is clear from the physical characteristics stated above that the motor electrical time constant is overwhelmingly lower than the mechanical time constant. According to the picture, the position control structure includes the RISC and servo motor transfer function. The conventional motor current feedback controller can avoid instantaneous current stress to the servo driver. This technology has been applied to the servo motor control to improve the control performance.θr=∫ωrdt
θm=2/Pθr

{x1(t)=x2(t)
{x2(t)=-a1x1(t)-a2x2(t)+bU(t)-TL(t)
RISC is a typical state feedback control scheme that combines an integral controller and the plant series state feedback information. The RISC function is expressed as follows, where and are the plant state variables and is the current compensator for the current feedback loops. The pulse width modulation (PWM) circuit mode can be simplified as a constant gain, where denotes the supply voltage; is the triangular waveform peak value. For a third RISC system, the control function can be expressed as follows:
U(s)=K1K2K3*θcmd(s)-x1(s)/s-K2K3x1-K3x2
Phase Tracking Control SchemeBefore the excitation synchronous generator system connects to the grid, equals the grid voltage angle. With the coaxial configuration described, the servo motor and generator electrical angle can be obtained using the motor encoder and the grid voltage sensor, respectively. The MCU compares the phase difference between the two signals and gradually adjusts the excitation synchronous generator rotor position to reduce the phase deviation.
Maximum Power Tracking Control
In a natural environment, wind power varies with time. To stabilize the generator output voltage, current, and output power, the excitation synchronous generator output power has to track the input power variation and react immediately by adjusting the excitation field current. In this paper, a maximum power tracking control scheme is proposed. The proposed MPTC scheme includes two control loops, which are the motor power control loop, and the generator power control loop. By MPTC scheme, can make the motor consumption power and most of the wind power can be transferred to the grid by the generator.
If an air dynamic occurs in the wind turbine, the servo motor responds to this change to maintain the generator speed constant. The three-phase servo motor power is calculated and compared to the servo motor command. In this state, the servo motor command is set equal to zero. The servo motor deviation signal command passes by the motor power control loop to obtain the signal. As is expected, in the steady state, the servo motor consumes less power.
In the generator power control loop, the three-phase voltages , and currents of the excitation synchronous generator power output are fed back for comparison with the generator power command. This power deviation passes the PI controller and the excitation gain generates a corresponding excitation field current control signal. Thus the excitation synchronous generator output power can track the generator power command.
Post a Comment:
You may also like:
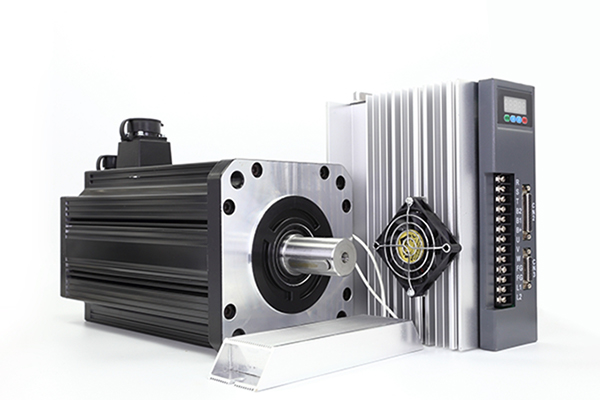
Category
Featured Articles
Servo Motor in Medical Industry
With the continuous development of technology, servo motors are being used more and more widely in medical equipment. Servo ...
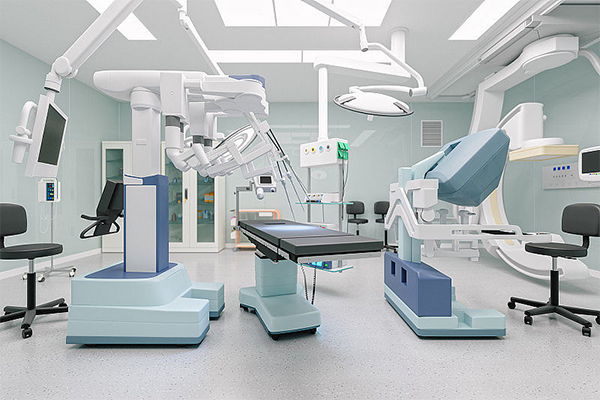
Servo System in CNC Machine Tools
As the actuator of CNC machine tools, servo system integrates power electronics, control, drive and protection, and with the ...
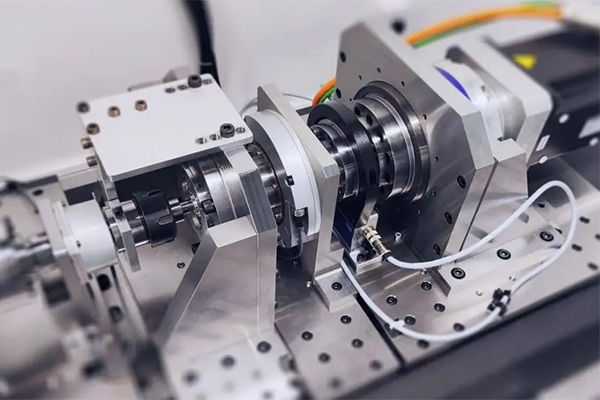
Equation Derivation for Servo Motor
In the analysis of electric servo drive motors , the equations for the motor indicates the presence of two time constants. One is ...
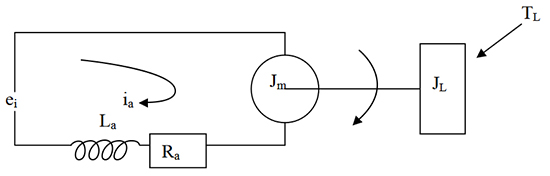
Servo Drives for Electric Mobility
Servo drives play a crucial role in electric mobility applications, providing precise control of electric motors for various ...
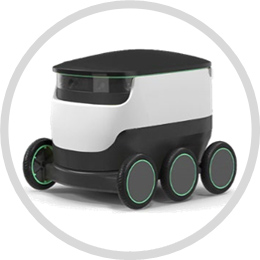
Servo Motor in Food Industry
In the ever-evolving landscape of the food industry, technological advancements play a pivotal role in enhancing efficiency, ...
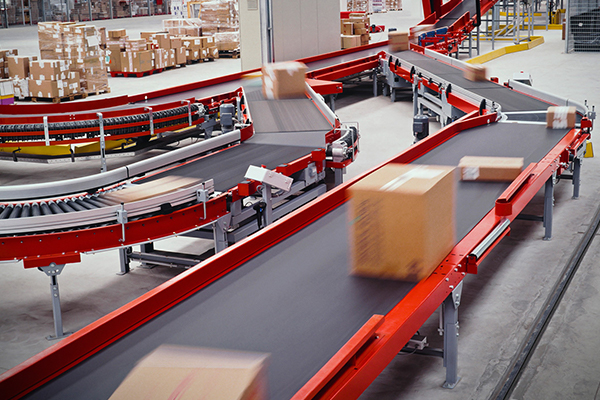