Servo motors play a crucial role in various industrial applications, offering precise control over motion and positioning. One essential concept in the realm of servo motors is inertia, a parameter that significantly influences their performance. In this article, we will delve into the distinctions between high and low inertia in servo motors, exploring their implications on system dynamics and overall efficiency.
A servo motor is a type of motor that allows precise control of position, speed, and acceleration through a controller. Servo motors usually consist of a motor, an encoder, and a controller. The controller adjusts the drive current of the motor according to the position information fed back from the encoder, thus controlling the position and motion of the servomotor. The following steps are generally required to utilize a servo motor.
Servo and proportional valves are used to precisely control the position or speed of an actuator. The valves are different internally but perform the same function. A servo valve normally utilizes an internal mechanical feedback device. Proportional valves usually have an electrical feedback, commonly called an LVDT.
Both valves operate from a variable DC signal. The command voltage input into the valve amplifier is usually + or -10 volts. The amplifier then converts the voltage into a current signal to drive the valve. Normally a positive voltage will shift the valve spool into the “A” position, a negative voltage will shift the valve spool into the “B” position. The valve spool shifts directly proportional to the strength of the command voltage. The higher the voltage the more oil can flow through the valve. The valve controls both the direction and speed of the actuator. Filtration to the servo valve is normally 3 microns.
Both valves operate from a variable DC signal. The command voltage input into the valve amplifier is usually + or -10 volts. The amplifier then converts the voltage into a current signal to drive the valve. Normally a positive voltage will shift the valve spool into the “A” position, a negative voltage will shift the valve spool into the “B” position. The valve spool shifts directly proportional to the strength of the command voltage. The higher the voltage the more oil can flow through the valve. The valve controls both the direction and speed of the actuator. Filtration to the servo valve is normally 3 microns.
RC Servos are very popular mechanisms in the world of RC models. No matter if this is a train model, or a car, or a boat, plane or helicopter, there must be at least one servo hidden somewhere within the constructions. RC Servos are used to convert electrical signal into polar or linear movement. A simple example is the steering system of an RC car. When signal is transmitted from the control to the car, this signal is decoded and sent to a servo. According to this signal, the servo will rotate it's drive shaft for some degrees, and this rotation is translated into wheel steering. The reason that makes those servos vary handy is that, they have a very easy (and universal) way of driving them with a simple PWM circuit, they can achieve from low to higher torques, enough to move almost everything needed in an RC model, they are very compact and reliable, and most of all, they come with very low prices according to their specifications.
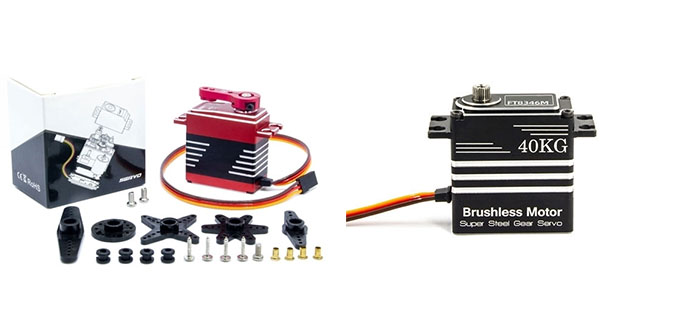
A micro servo motor is a motor that is powered by a DC power source (from an external power source or controller). A miniature servo motor that is small, lightweight and has a high power output is known as a micro mini servo motor. This means that a miniature micro servo motor will only work hard to accomplish the task at hand. Servomotors have a wide range of applications including cameras, telescopes, antennas, industrial automation and robotics. The motors rotate from 0 to 180 degrees at each 90 degree position, inby named. Servomotors have a gear that reduces the speed of the motor by decreasing the speed and increasing the torque.

Servo motor is a kind of motor that can realize precise control and position feedback, and its transmission mode plays a crucial role in the performance and application scenario of the motor. In this paper, we will discuss the principle, characteristics and application of servo motor transmission mode from the perspective of its transmission mode.
Servo motors are also called actuator motors, or control motors. In automatic control system, servo motor is an executive element, its role is to transform the signal (control voltage or phase) into mechanical displacement, that is, to change the received electrical signal into a certain speed or angular displacement of the motor. Its capacity is generally 0.1-100W, commonly used is below 30W. Servo motors are divided into DC and AC.
Today we will learn to control a servomotor. We'll use a continuous rotation servo, which makes our servo motor rock-and-roll. The control procedure that we will learn is also applicable to any servo motor.
The external controller controls the servo system through a signal called PPM code modulation to avoid confusion with pulse width modulation. A control wire communicates the desired angular movement to the servo. The angle is determined by the duration of the pulse applied to the control wire.
PPM uses 1 to 2ms out of a 20ms time period to encode its information. The servo expects to see a pulse every 20 milliseconds (02 seconds). The length of the pulse will determine how far the motor turns. A 1.5-millisecond pulse will make the motor turn to the 90-degree position (often called the neutral position). If the pulse is shorter than 1.5ms, then the motor will turn the shaft closer to 0 degrees. If the pulse is longer than 1.5ms, the shaft turns closer to 180 degrees.
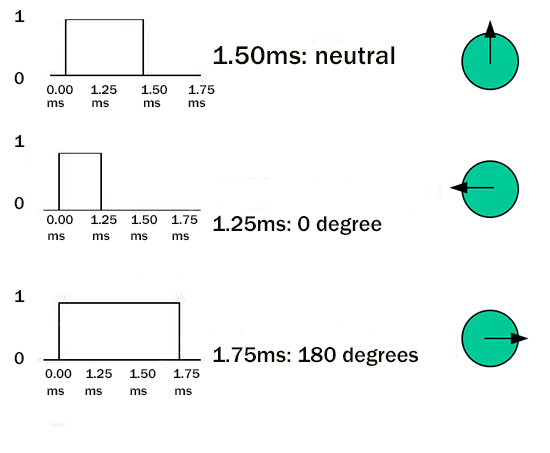
The external controller controls the servo system through a signal called PPM code modulation to avoid confusion with pulse width modulation. A control wire communicates the desired angular movement to the servo. The angle is determined by the duration of the pulse applied to the control wire.
PPM uses 1 to 2ms out of a 20ms time period to encode its information. The servo expects to see a pulse every 20 milliseconds (02 seconds). The length of the pulse will determine how far the motor turns. A 1.5-millisecond pulse will make the motor turn to the 90-degree position (often called the neutral position). If the pulse is shorter than 1.5ms, then the motor will turn the shaft closer to 0 degrees. If the pulse is longer than 1.5ms, the shaft turns closer to 180 degrees.
Servo motors are devices that convert electrical signals into mechanical motion and are widely used in industrial automation, robotics, aerospace and other fields. In order to ensure the stability and performance of servo motors, a series of test methods are required. In this paper, we will introduce the test methods of servo motors and elaborate each test step in detail. The test methods of servo motors mainly include two parts: static test and dynamic test.
There are some special types of application of electrical motor where rotation of the motor is required for just a certain angle not continuously for long period of time. For these applications, some special types of motor are required with some special arrangement which makes the motor to rotate a certain angle for a given electrical input (signal). This is normally a simple motor which is controlled for specific angular rotation with the help of additional servomechanism (a typical closed loop feedback control system). Servo motor is a special type of motor which is automatically operated up to certain limit for a given command with help of error-sensing feedback to correct the performance.

Servo motors play a crucial role in various industries, serving as precision control devices in applications ranging from robotics to manufacturing processes. To ensure optimal performance and longevity, it is essential to implement a systematic maintenance routine. In this article, we will explore the key steps and best practices for maintaining servo motors.
It's important to consider the unique demands of a motion control application when selecting a power supply. During accelerations, motor drives can quickly draw large amounts of power. Additionally, motors can create regenerative energy and push current back into the power supply during deceleration, which means the power supply needs to handle the resulting increase in voltage. Highly dynamic motion applications place large and rapid demands for current on the power supply.
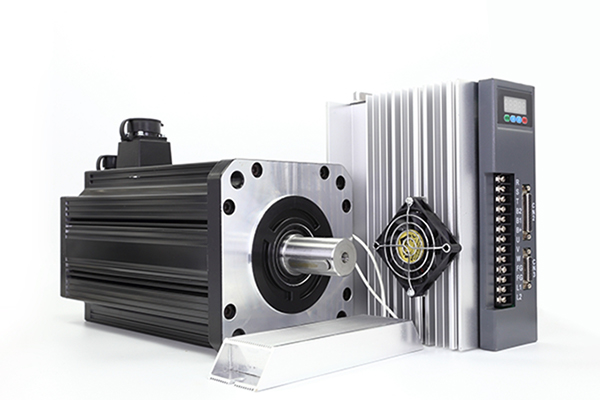
Category
Featured Articles
What is a Servo Motor?
There are some special types of application of electrical motor where rotation of the motor is required for just a certain angle ...
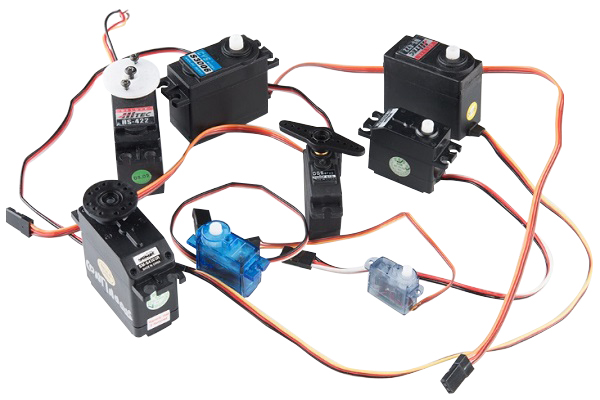
How to Test Servo Motor?
Servo motors are devices that convert electrical signals into mechanical motion and are widely used in industrial automation, ...

What are the Types of Servo Motor?
There are some special types of application of electrical motor where rotation of the motor is required for just a certain angle ...

How to Maintain Servo Motor?
Servo motors play a crucial role in various industries, serving as precision control devices in applications ranging from ...

How to Select the Suitable Power ...
It's important to consider the unique demands of a motion control application when selecting a power supply. During ...
