Home » AC Servo Motor » AC Servo Motor Installation Instruction
AC Servo Motor Installation Instruction
AC servo motor is a very important part of
the AC servo system. AC servo motors play a key role in automation systems, so
correct installation is critical to system performance and stability. Please observe the installation
instructions described below to install the servo motor correctly.

Before installation

- Anti-corrosive paint is coated on the edge of the servo motor shaft. Clean off the anti-corrosive paint thoroughly and use a cloth moistened with thinner. Avoid getting thinner on other parts of the servo motor when cleaning the shaft.
- Before installation, we should check whether the model, specification and function of the motor are in accordance with the design requirements to ensure that the quality and performance of the motor to ensure that the quality and performance of the motor can meet the requirements of use.
- The motor should be installed on a solid foundation, and ensure that the cable connection between the motor and the drive is firm and reliable.
- During the installation process, to avoid the motor to be impact and vibration impact, so as not to damage the motor or affect its performance.
- During the commissioning process, the position, speed and acceleration of the motor should be precisely adjusted to ensure that its coordination and performance with the driver are optimized.
- After the installation is completed, the motor should be comprehensively checked and test to ensure that it can work normally and meet the design requirements.
Storage
When the servo motor is not being used, store it in an area with a temperature between -25°C and 60°C with the power cable disconnected.
Installation Orientation
Installation sites
Align the axis of the servo motor with the axis of the machinery to be controlled. Then connect the two shafts with a flexible coupling. Measure the distance at four different positions around the circumference. The difference between the maximum and minimum measurements must be less than or equal to 0.03 mm. (rotated with the coupling). Motor mounting base accuracy, screw circumferential run out, coupling circumferential run out, and the deviation of the screw from the motor shaft core all affect the mounting accuracy of the servomotor, and the accuracy of each needs to be ≤ 10μm.
(Note: If the alignment accuracy is incorrect, vibration will occur, resulting in damage to the bearings. Mechanical shock to the shaft end is forbidden, otherwise, it may result in damage to the encoder of the servo motor.)
Handling oil and water
If the servo motor is used in a location that is subject to water or oil drops, make sure of the servo motor's protective specification. If the servo motor is required to meet the protective specification of the through shaft section by default, use a servo motor with an oil seal.
Cable connection
When connecting the cables, the bending radius should not be too small, do not bend or apply tension to cables. Since the conductor of a signal cable is very thin (0.2 mm or 0.3 mm), handle it with adequate care.
When the servo motor is not being used, store it in an area with a temperature between -25°C and 60°C with the power cable disconnected.
Installation Orientation
Servomotors can be mounted horizontally or vertically with the motor shaft oriented in the same direction as the machine shaft. When mounting an standard AC servo, the direction of the motor shaft should be the same as the direction of the mechanical shaft. This is to ensure that the motor operates properly and does not cause problems such as stalling or abnormal wear. If the direction of the motor shaft is not consistent with the direction of the mechanical shaft, it may lead to a mismatch between the motor and the mechanical load, affecting the performance and life of the motor.
Installation sites
- The servo motor is designed for indoor use. Install the servo motor in an environment that meets the following conditions.
-
Free from corrosive and explosive gases.
-
Well-ventilated and free from dust and moisture.
-
Ambient temperature from 0 to 40C.
-
Relative humidity from 26% to 80% (non-condensing).
-
Facilitates inspection and cleaning.
-
Ensure that the servo drive and motor, power lines and other equipment to maintain the appropriate distance height to avoid overheating and possible electrical interference.
-
Ensure that the installation platform is flat and stable to prevent vibration and potential physical damage.
Align the axis of the servo motor with the axis of the machinery to be controlled. Then connect the two shafts with a flexible coupling. Measure the distance at four different positions around the circumference. The difference between the maximum and minimum measurements must be less than or equal to 0.03 mm. (rotated with the coupling). Motor mounting base accuracy, screw circumferential run out, coupling circumferential run out, and the deviation of the screw from the motor shaft core all affect the mounting accuracy of the servomotor, and the accuracy of each needs to be ≤ 10μm.
(Note: If the alignment accuracy is incorrect, vibration will occur, resulting in damage to the bearings. Mechanical shock to the shaft end is forbidden, otherwise, it may result in damage to the encoder of the servo motor.)
Handling oil and water
If the servo motor is used in a location that is subject to water or oil drops, make sure of the servo motor's protective specification. If the servo motor is required to meet the protective specification of the through shaft section by default, use a servo motor with an oil seal.
Cable connection
- The cables connected to the servo drive should use appropriate shielded cables to prevent electromagnetic interference.
-
Cable connections must be correct and secure to avoid overheating and potential electrical failures.
-
Use appropriate terminals and connectors to connect cables as needed.
- According to the model and specifications of the servo drive, use the corresponding software for configuration and control.
-
Make sure the communication settings between the computer and the servo drive are correct, including communication protocol, baud rate, data bits, etc.
-
Configure and adjust the parameters of the servo drive as needed to meet application requirements.
When connecting the cables, the bending radius should not be too small, do not bend or apply tension to cables. Since the conductor of a signal cable is very thin (0.2 mm or 0.3 mm), handle it with adequate care.
Post a Comment:
You may also like:
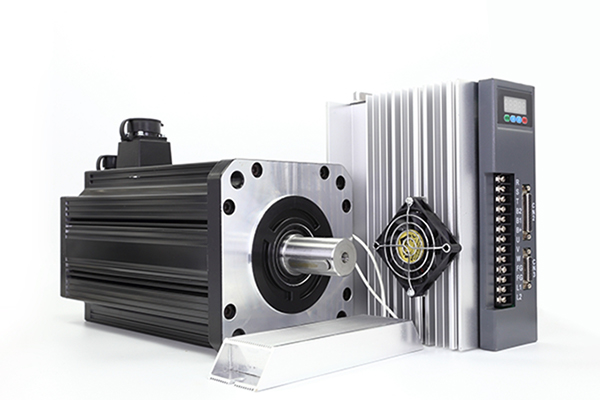
Category
Featured Articles
What is Operation Principle of AC ...
The output torque of the servo motor is proportional to the current that flows in the motor. Because the servo amplifier normally ...

What is Position Control by AC Servo?
The methods for stopping a moving object with prescribed accuracy at a fixed position consist of a mechanical method and an ...

AC Servo Motor: Structure, Working and ...
AC servo motor is a type of motor widely used in various industrial and commercial fields. It features high precision,fast ...

How to Wire an AC Servo Motor?
A servo motor is a type of motor that allows precise control of position, speed, and acceleration through a controller. The ...
